News
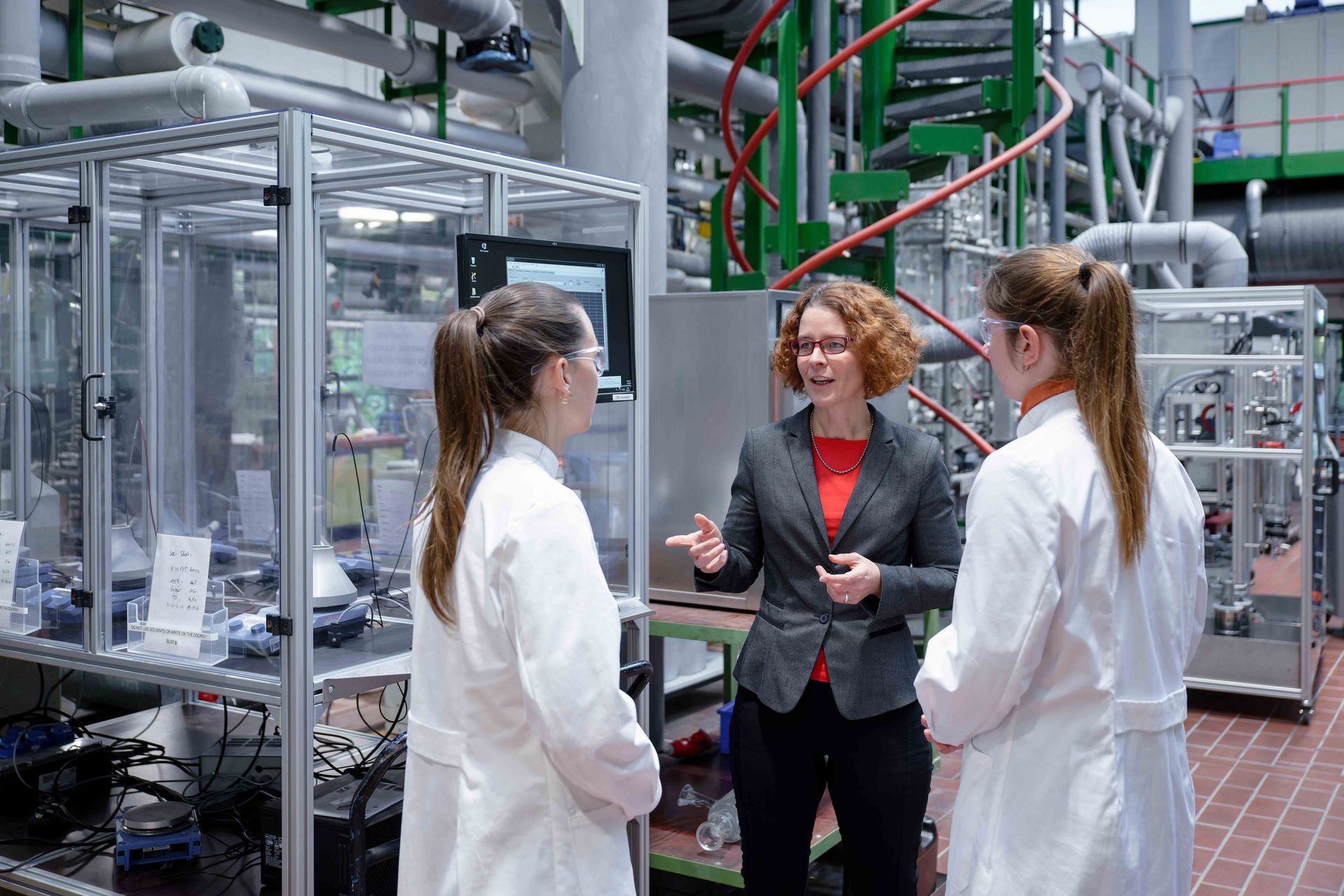
A multidimensional circular economy
Converting plastic waste into versatile, high-quality chemical building blocks: researchers in the WSS100 final project “catalaix” want to develop catalysis-driven recycling processes that enable a multidimensional circular economy.
Packaging, insulation materials, textiles, fertilisers, pharmaceutical products: it’s impossible to imagine modern life without the products created in the chemical industry. Unfortunately, however, most of these products are thrown away at the end of their life cycle. The plastics industry provides ample evidence that something has to change: humans produce four hundred million metric tonnes of plastic per year—by 2050, it will most likely rise to sixteen gigatonnes, which is the combined weight of all humans, animals and fungi living on the planet. The manufacture of plastics consumes huge amounts of energy, causes massive CO2 emissions and leaves behind mountains of waste.
For their WSS100 proposal, the team led by Jürgen Klankermayer and Regina Palkovits at the Rhein-Westphalian Technical University Aachen developed a concept that can convert these kinds of waste streams into valuable, reusable resources. Their idea revolves around catalysis—the technology that accelerates the speed of chemical reactions. “Up to now, chemists have mainly sought new catalysts that create bonds,” Jürgen Klankermayer explains. “But we also need catalysts that break bonds down, and we have to start thinking about recycling plastics already during the production phase.”


Linking cycles
Today, only nine percent of all plastics are recycled; examples include PET bottles that are shredded and remade as new PET bottles. However, Regina Palkovits points out, these kinds of one-dimensional cycles are unsuitable for a holistic approach. “Different plastics are produced in different amounts. And they also have different lifespans: whereas packaging should perhaps be reintegrated into the cycle already after six months, the period is thirty years for building insulation.”
The catalaix project team propose creating a multidimensional circular economy with an open-loop principle. This means that the molecular building blocks made using catalysis-driven recycling can be used in so many different ways that they could be channelled into other value chains and material cycles as needed. “This will enable the linking of previously isolated cycles of matter and the development of a flexible circular economy,” Jürgen Klankermayer says.
Regina Palkovits adds that it’s also important to look at waste products as valuable resources. That’s why the researchers want to produce molecular building blocks during recycling that retain the greatest possible chemical value. “We don’t want to completely break down plastics into synthesis gas or burn them down to CO2. We only want to go so far as to make them usable in a wide range of applications.” These future building blocks should also be more environmentally friendly, ideally even biodegradable. “There’s absolutely no point in producing yet another project that’s difficult to recycle,” Palkovits says.
Converting polyethylene into polylactic acid
With the money from the WSS research prize, the catalaix team have already used models to demonstrate the possibilities of a multidimensional circular economy. The researchers developed a new catalytic process to convert polyethylene into the biodegradable polylactic acid by adding biomass. However, a single procedure isn’t nearly enough to attain the researchers’ ambitious goal. Especially as there are some two hundred classes of plastics on the market today.
Further complicating the issue is the fact that plastics are often not used in their pure form: instead, they’re combined with stabilisers, flame retardants and dyes as well as additives like plasticisers to make them soft. “In the research lab, there’s a tendency to work with very pure materials or with model compounds,” Jürgen Klankermayer says. “But to have an industrial impact, our catalysts need to function in real-world materials. That’s the critical step.”
Molecules, materials, systems
The researchers have proven they can do just that in an experiment with a PET bottle: they broke down the PET polymer into a reusable building block—and in the process also removed Bisphenol A, a plasticiser that makes the bottles pliable. Indeed, this conversion of the plasticiser via biocatalysis methods is representative of just how remarkable the catalaix team’s approach is. “Our work is interdisciplinary,” Regina Palkovits says. “Depending on the specific material and the starting point, we’ll choose very different catalysis methods.”
From the very start, the team have been focused on the practical application of their method. In addition to examining the individual molecules and the materials, including all components, they also study the manufacture processes down to the economic and logistics systems where plastics are found. Responsible for this work are researchers in the field of process engineering, who make various assessments already at an early stage: for instance, they determine whether a catalysis can be integrated into an industrial process, or they identify the material balance and energy requirements. In addition, specialists in sustainability and system evaluations assess what newly created molecules could prove to be sustainable and in-demand on the market. All necessary steps—because researchers in the catalaix project aim to do no less than pave the way for a sustainable chemical industry.

