News
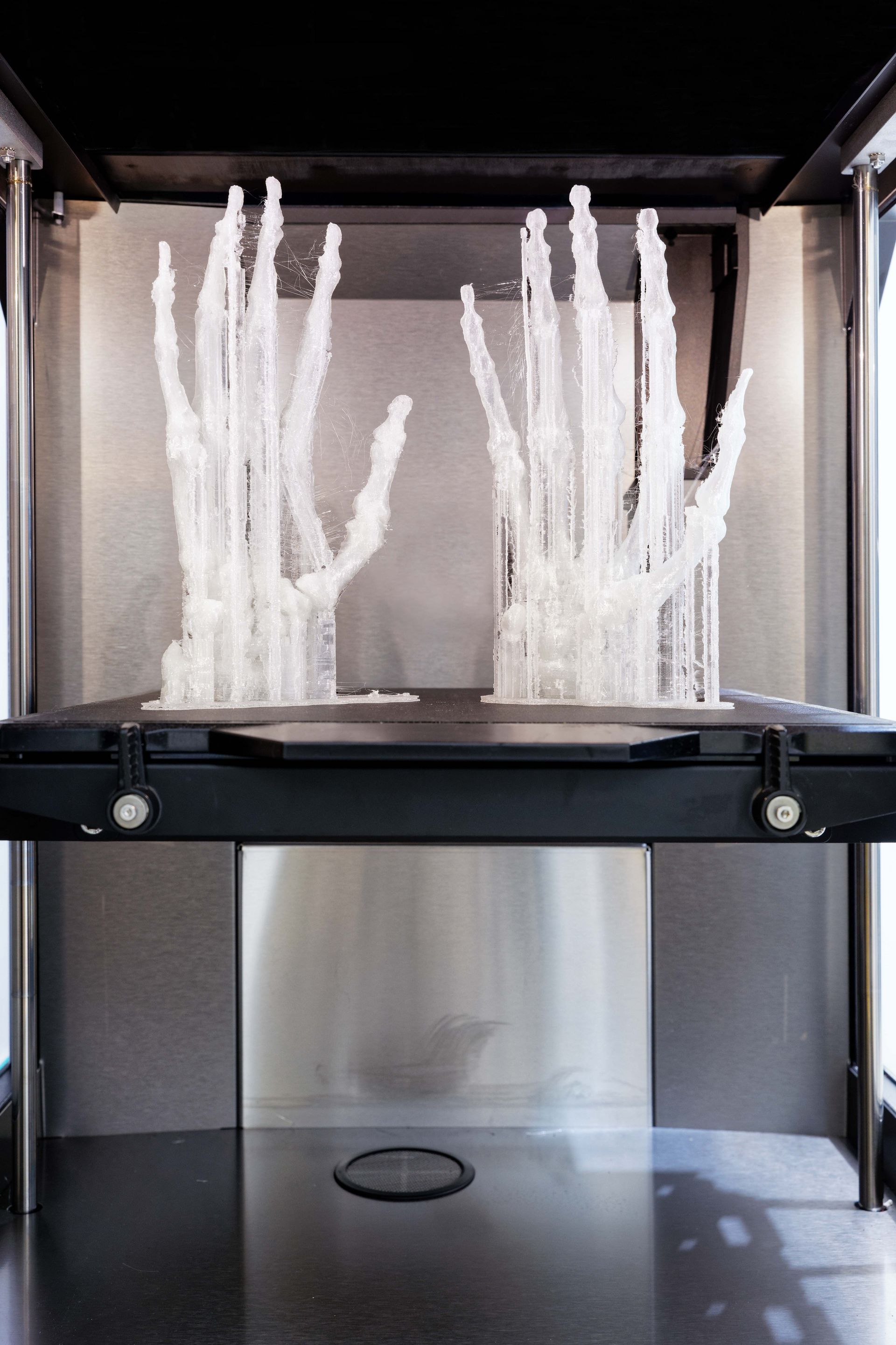
Implants from the printer
What properties must an implant have to promote gentle, effective healing in bones? This is the question being addressed by the MIRACLE II research group “Smart Implants” led by Florian Thieringer. The oral and cranio-maxillofacial surgeon is establishing a platform at the University Hospital Basel to provide patients with smart, 3D-printed bone implants that are made to measure. A conversation with the new co-leader of the MIRACLE II project.
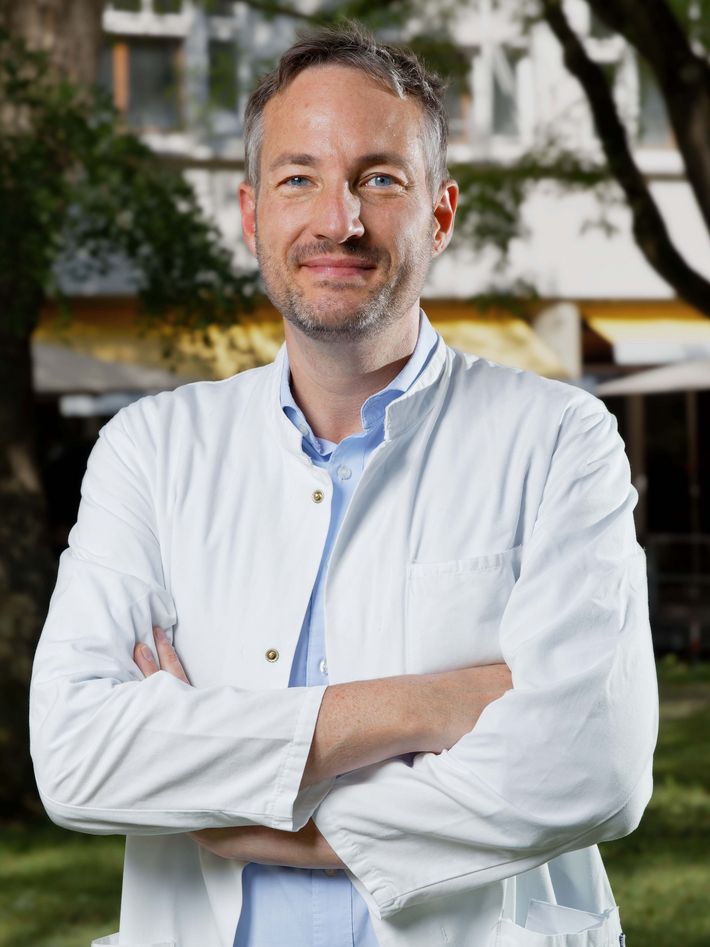
Florian Thieringer, with the launch of MIRACLE II, you have taken over the role of project co-leader from Hans-Florian Zeilhofer, who has since been conferred emeritus status. How did you come to join the team?
Florian Thieringer: In the early 2000s, I was studying with Hans-Florian Zeilhofer just as his group started researching how 3D-printed implants could be used to simplify complex operations. One of the most important things I learned in my twenty years of work with him was this: when developing new methods, cross-disciplinary collaboration is indispensable. That’s why it was important to the MIRACLE II team to keep a clinician who regularly operates on patients in the project.
You’re developing 3D printing methods to produce bone implants. Why?
With 3D printers, we can produce implants that are made to measure for an individual patient and a specific operation. We can then use minimally invasive techniques to insert them in the body. For example, I recently operated on a patient whose jawbone had to be stabilised following damage by a tumour. Based on the patient’s CT scans, we were able to design a sleek 3D-printed titanium implant that we could insert directly through the oral cavity, without making any cuts to the face. Smart implants can potentially replace standard implants in many other surgical procedures, too, allowing for minimally invasive procedures that are gentler on the patient.

Are customised implants already in regular use?
Yes, but until now, hospitals, including the University Hospital Basel, have had to order made-to-measure implants from external firms—an expensive and time-consuming process. We want to change that by making customised implants routinely available at our hospital. To this end, we recently purchased a new 3D printer for our in-house 3D Print Lab. It’s a big machine that prints using PEEK (polyether ether ketone), a high-performance polymer that we’ve researched intensively in recent years as a material for implants. Beginning in 2022, we’ll already be able to produce tailor-made implants in just a few hours—and that close to the operating theatre, directly at the point of care. This way, we can integrate smart implants seamlessly into existing treatment processes to benefit as many patients as possible. This approach has already proven successful with the other equipment in our 3D Print Lab.
What have the 3D printers already been used for?
At the University Hospital Basel, we already use our 3D Print Lab to produce surgical templates and patient-specific anatomical models. Such models are excellent tools when planning operations and discussing procedures with patients. Indeed, 3D-printed models are extremely valuable in both medical education and surgical planning: when doctors hold a three-dimensional model in their hands, they literally grasp—in both senses of the word—a patient’s anatomy. Because the 3D Print Lab is now integrated in the treatment processes, physicians can order the required models directly in the central patient information system. In addition, future physicians at the University Hospital already learn during their studies how to translate data from imaging techniques like CT and MRI into a 3D rendering that can be printed. As such, 3D printing has become a standard procedure for us.

What are the next steps?
We’re working on various approaches. For instance, we want to investigate the potential of 3D-printed implants in other applications—trauma surgery involving face or head injuries to name one example. Until now, it’s taken too long for patient-specific implants to be fabricated and delivered. With our new 3D printer, however, we can make such applications possible. We’re also conducting research with the Swiss Federal Institute of Technology Zurich (ETH Zurich) to learn how we can make implants even smaller. Our idea is to fold them like origami figures, allowing us to use the least invasive interventions possible when inserting them in the body. In future, we also want to conduct in-depth research on biological implants. In particular, we want to develop net- or honey-comb-like structures over which bone tissue can regrow and which could be used to promote regeneration in patients who have lost bone mass due to infections. These kinds of bioimplants could even be produced from materials that, after a certain time, are absorbed by the body—in other words, the implants naturally decompose when the patient no longer needs them.
Text: Santina Russo
Photos: Oliver Lang
