News
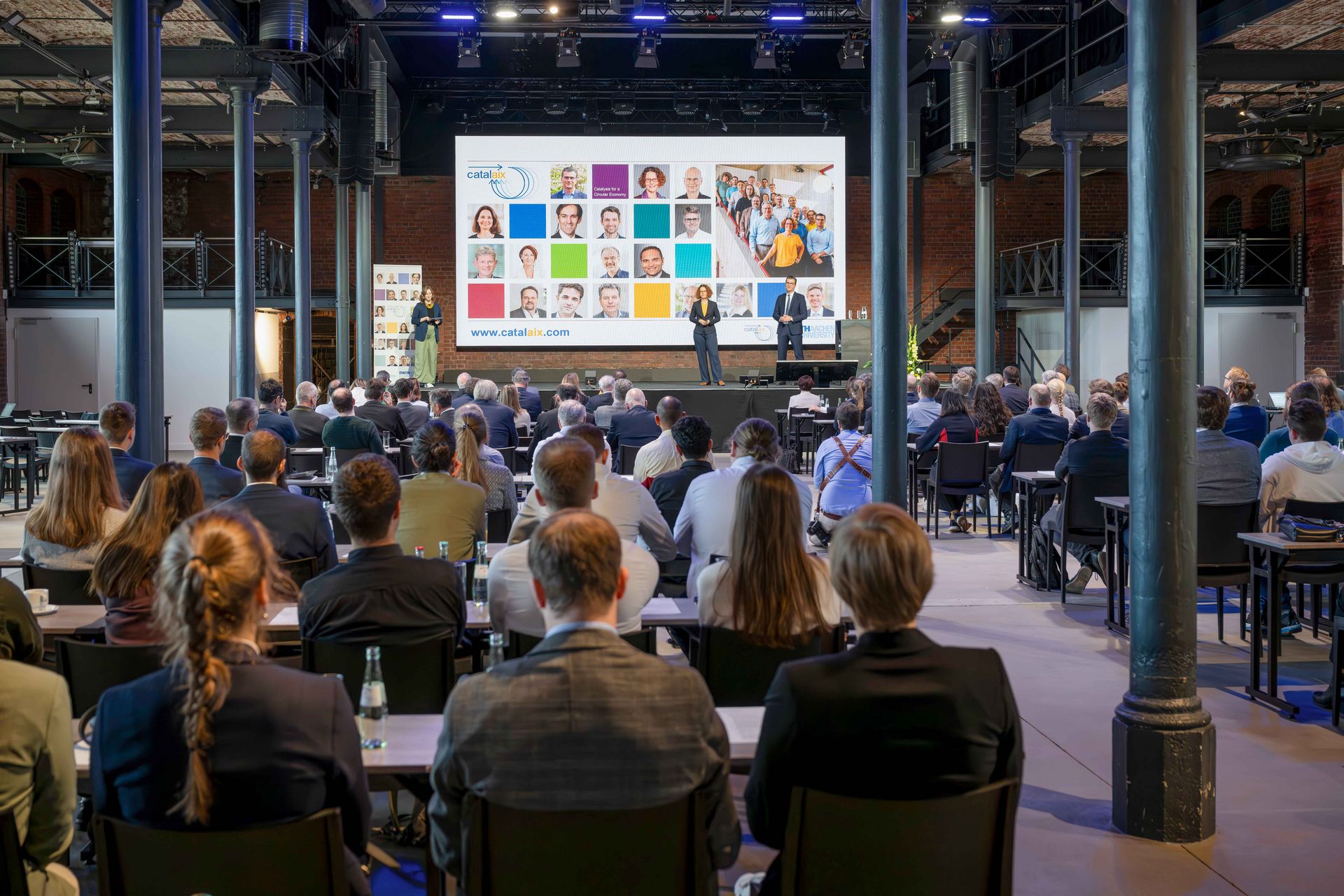
Let the adventure begin
At the end of September, some two hundred guests arrived in Aachen, Germany, to celebrate the new “catalaix” WSS Research Centre. Endowed with a grant of one hundred million Swiss francs from the Werner Siemens Foundation, the bold endeavour is aiming to break down plastics into their individual components—creating the basis for a multidimensional circular economy.
Professors Regina Palkovits and Jürgen Klankermayer, heads of the “catalaix” WSS Research Centre in Aachen, invited some two hundred guests from the worlds of politics, industry and academia to celebrate the start of their pioneering project that—as the winner of the Werner Siemens Foundation project-of-the-century competition to celebrate its centennial anniversary—received a ten-year grant of one hundred million Swiss francs.
Siemens Family Advisory Board Member Christina Ezrahi congratulated the researchers on behalf of the Foundation. She said the project’s aim to make the plastics industry more sustainable would have earned Werner Siemens’s full approval, as he attached great importance to solving problems through innovation—and she cited her distinguished ancestor: “The value of an invention lies in its practical realisation.”
Sibylle Keupen, mayor of Aachen, also offered her congratulations, as did Ulrich Rüdiger, rector of RWTH Aachen University. Both stressed the importance catalaix has for the city of Aachen and its university. “The project will lead to the foundation of innovative start-ups,” Sibylle Keupen said, “and that will have a positive impact on the city.” For his part, Ulrich Rüdiger pointed out that researchers have a responsibility to explore pioneering new pathways—and that the catalaix team are doing just that.
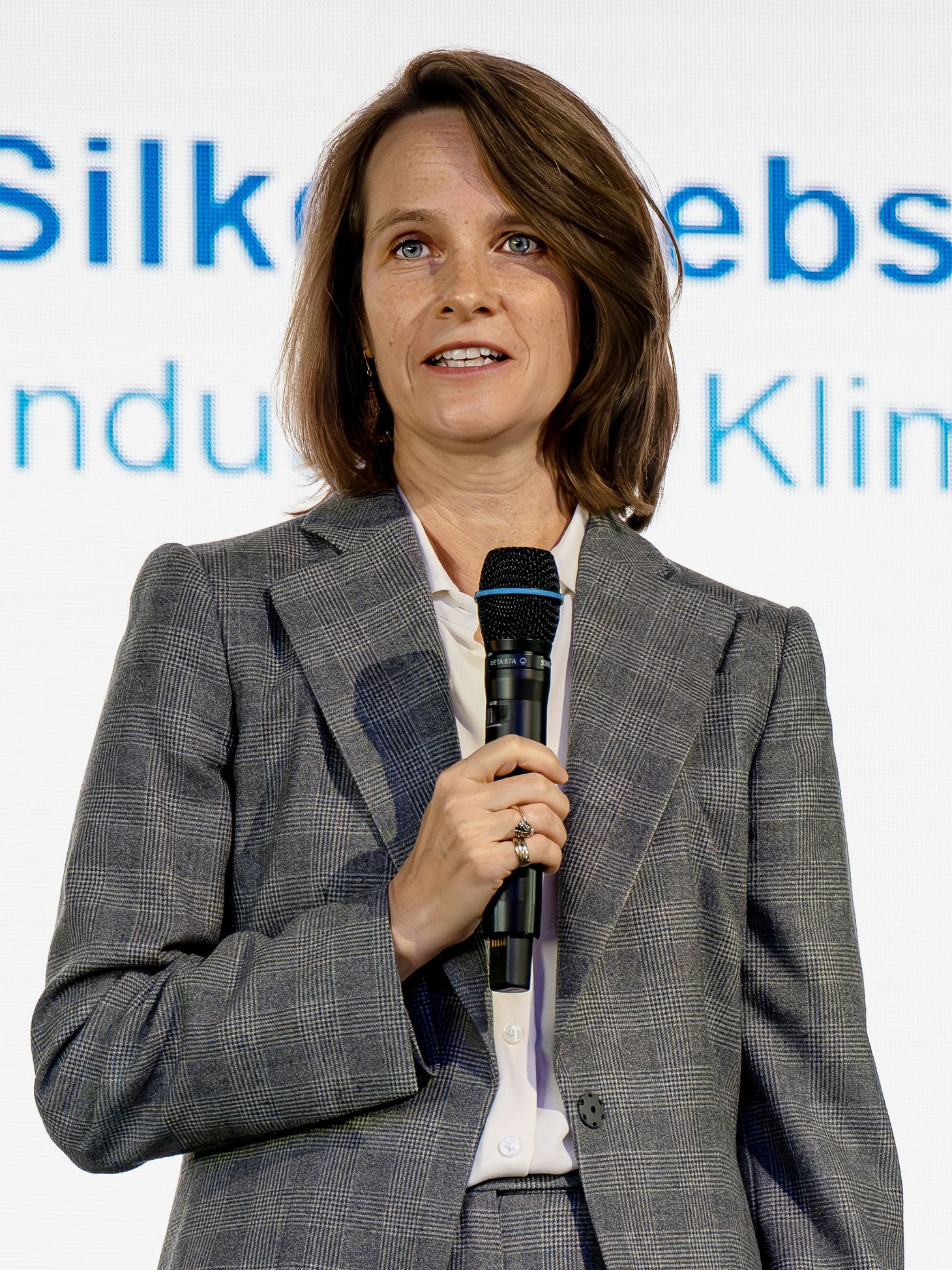
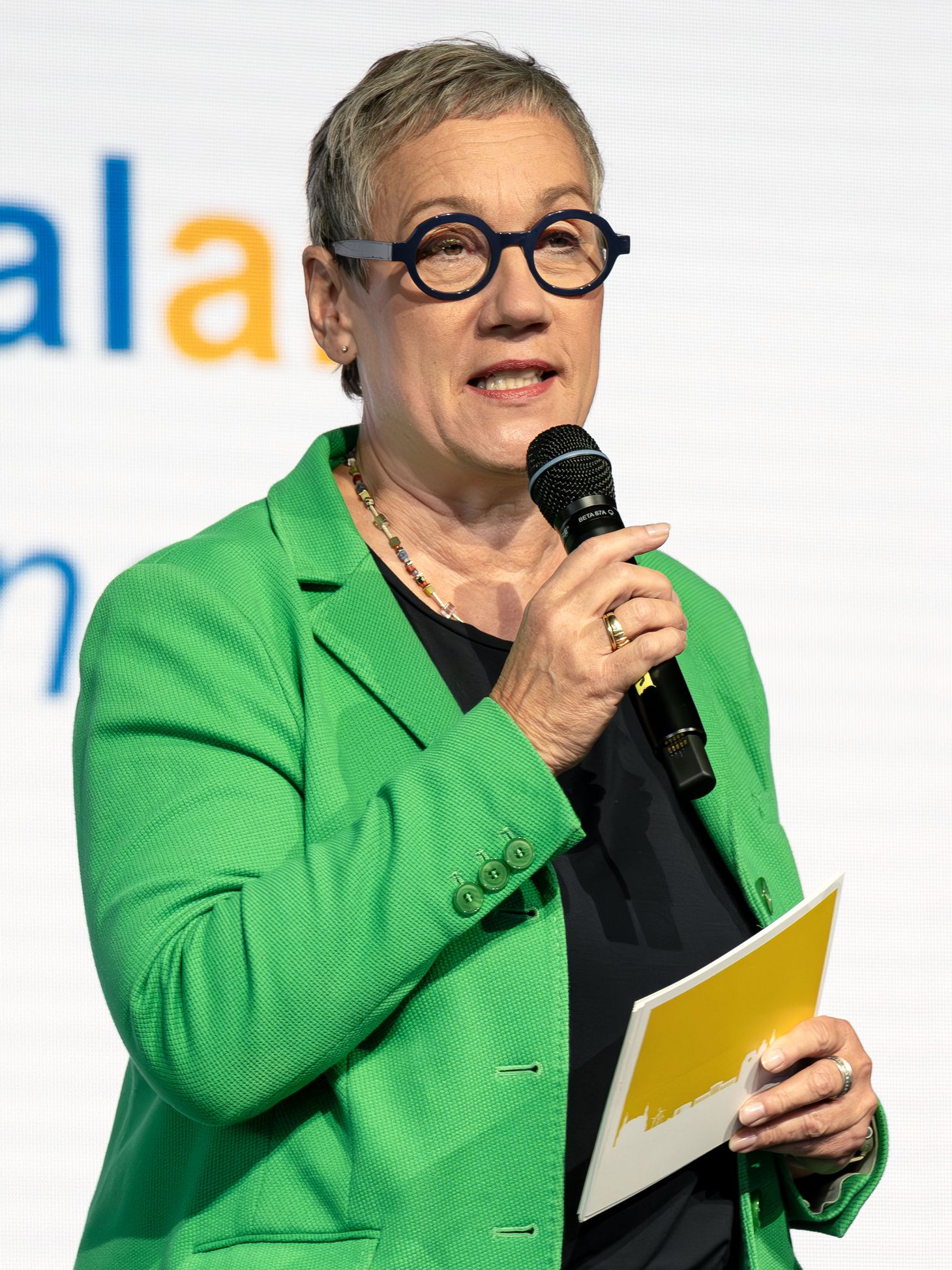
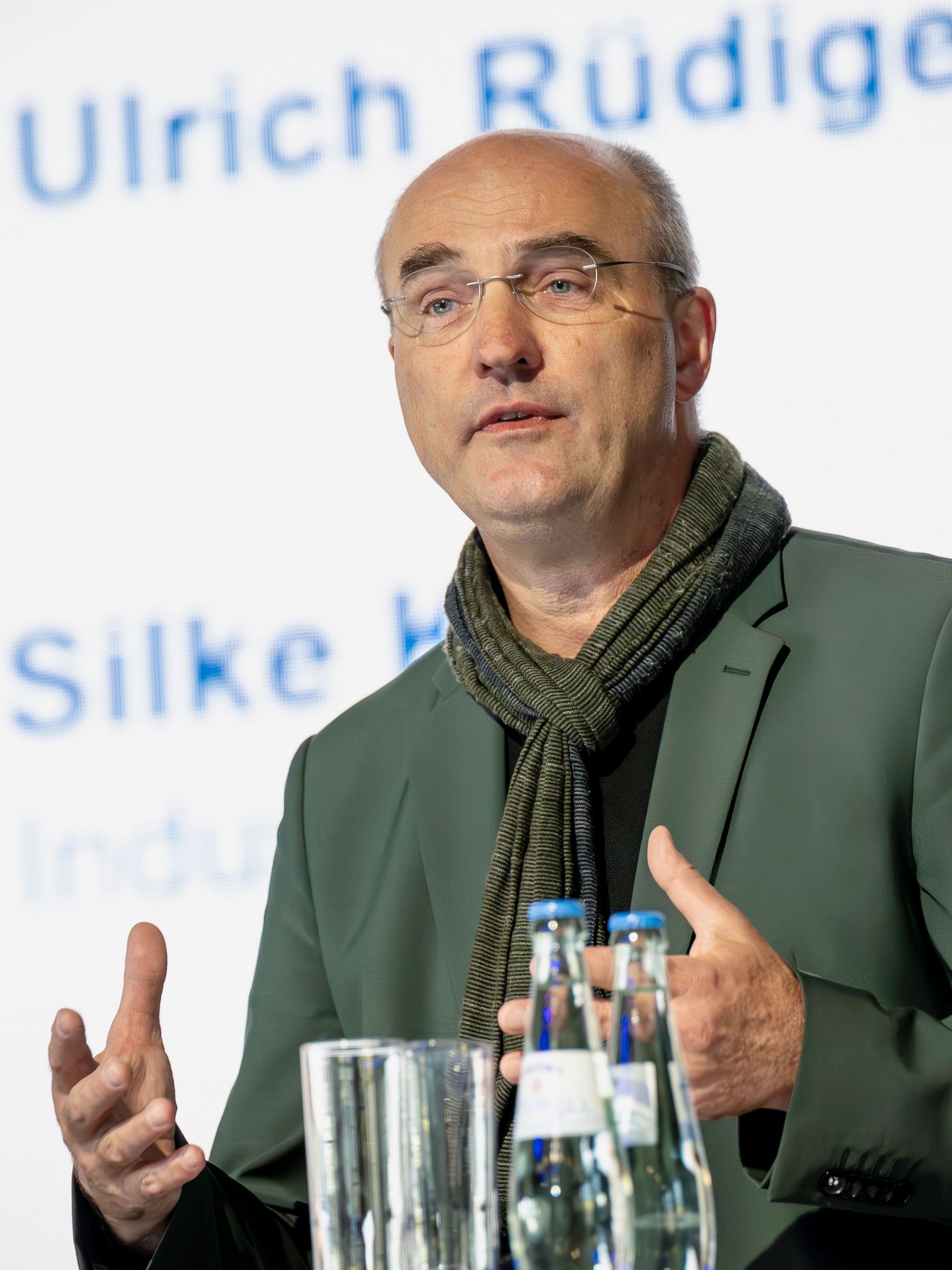
Ending one-dimensional production lines
Regina Palkovits and Jürgen Klankermayer then introduced the research centre and its foundational idea. In his presentation, Klankermayer spoke about the significance of the chemical industry, explaining that, at present, non-renewable energy carriers like petroleum and natural gas are used to manufacture all kinds of products that have become indispensable in our daily lives. Indeed, plastic production is a major branch of the chemical industry, with four hundred and thirty million metric tons of the material produced every year. By 2050, that could already rise to a gigaton.
The big drawback is that most of these materials—manufactured in complex and expensive processes—either end up in a landfill or are incinerated. “It’s a one-dimensional production line”, Klankermayer explained, adding that, at present, only some ten percent of all plastics are recycled. And this is precisely what the team at the WSS Research Centre plan to change: they want to use chemistry-based recycling processes to manufacture high-quality products. “Our idea is to convert plastic waste into a recyclable material,” Klankermayer said.
The central tool in their plan is catalysis: the process in which a chemical reaction is accelerated, or made possible in the first place. To date, as Klankermayer explained, catalysis has been used mainly to form bonds. “But now, we also want to break down chemical bonds.” Indeed, the researchers want to create such custom-made reactions that the resulting materials can be fed into a multidimensional circular economy. This way, plastic products would no longer simply be broken down into their smallest components; rather, they would be transformed into materials suitable for use in various production chains.
In her talk, Regina Palkovits highlighted the key role catalysts have in these processes, citing several examples in which researchers have demonstrated how monomers can be produced with a low-carbon footprint via catalytic pathways. And, she continued, with the seventeen research groups working at the WSS Research Centre, the whole range of catalysis techniques will be used. And so catalaix—a portmanteau of catalysis and Aix-la-Chapelle (the French name for Aachen)—is paving the way for a sustainable chemical industry.
Floating plastic islands
One of the major problems the catalaix project will help solve is plastic pollution in the environment—first and foremost in the world’s oceans. Steffen Knodt, board member of the German Association for Marine Technology, illustrated just how big the islands of plastic waste have grown, saying around two percent of used plastic lands in the ocean, which comes to roughly eight million metric tons per year. “By 2050, there will be about as much plastic in the ocean as there are fish.”
Fishing nets and other plastics in the fishing industry make up a large and very harmful percentage of the waste, while half is the result of disposable packaging. And, he continued, one of the most common plastic products found in the seas are plastic caps from bottles. There are now seven huge plastic islands that have been formed by currents within ocean gyres, and, as Knodt said, while methods have been devised to retrieve the rubbish, they are very expensive. “It would cost an estimated 7.5 billion dollars to clean up just one of the 7 islands.”
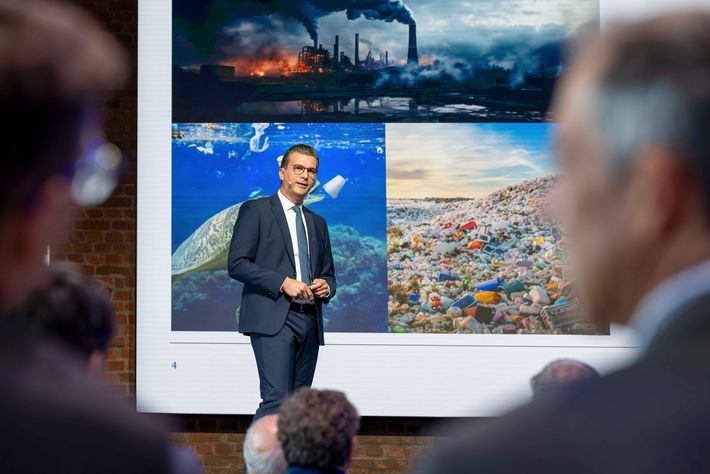

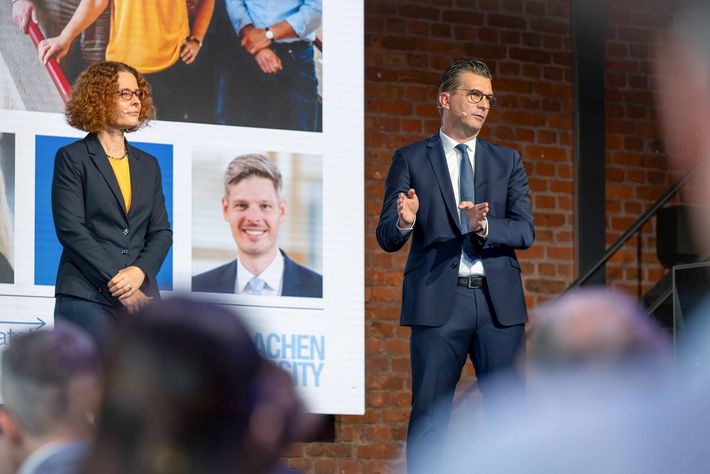
A big challenge
The afternoon was reserved for expert presentations on chances and challenges of the project. In a talk about why catalaix is essential for our planet, André Bardow, professor of energy and process systems engineering at ETH Zurich, documented exactly how incredibly difficult it is to create a climate-neutral plastics industry. Bardow’s research has shown that large quantities of biomass and renewable energies are needed—in addition to a recycling rate of at least seventy-five percent.
At the same time, he also warned his fellow researchers at the new WSS Research Centre against restricting their focus to the development of new catalysts. This, because apart from good catalysts, two other aspects are critical: enough raw materials and a cost-effective production process. “Without these features, a fantastic catalyst is nothing but an unprofitable piece of artistry.”
In his presentation, Bert Weckhuysen, professor of inorganic chemistry and catalysis at Utrecht University, focused on the refineries of the future where chemical products will be created not from petroleum but from plastic waste and renewable energies. New catalysts play a decisive role, as do new processes, new chemical reactors—and a lot of space and resources for wind turbines and solar panels.
Taking the long view
The last short presentations given by five catalaix group leaders demonstrated two main points: the work is already moving forward quickly—and the researchers are very aware that made-to-measure catalysts alone won’t solve the problem. Indeed, they must also develop scalable processes that work even with high production volumes. To enable these critical features, the make-up of the team is decidedly interdisciplinary, and the participating researchers cover each and every step: from the chemistry lab to the pilot plant, on to value chains for the resulting products. “Translation is a crucial aspect,” Regina Palkovits explained, “because we want to speed up the ideas coming from the lab and then move from experiment to marketable prototype.”
In a round table discussion, Professor Matthias Kleiner, member of the WSS Scientific Advisory Board and project leader of the WSS project of the century, was asked about what makes the catalaix project so unique. He answered that it was the courage to tackle as big a problem as the one-dimensional, petroleum-based plastics industry and its negative impacts. He also said that it’s unrealistic to think the project will have achieved all its aims by the end of the ten-year funding period. “We’re at the beginning of a long-term development,” Kleiner explained. “But I also hope that, in ten years’ time, we’ve reached the point where plastic recyclables have become an established line of business.”
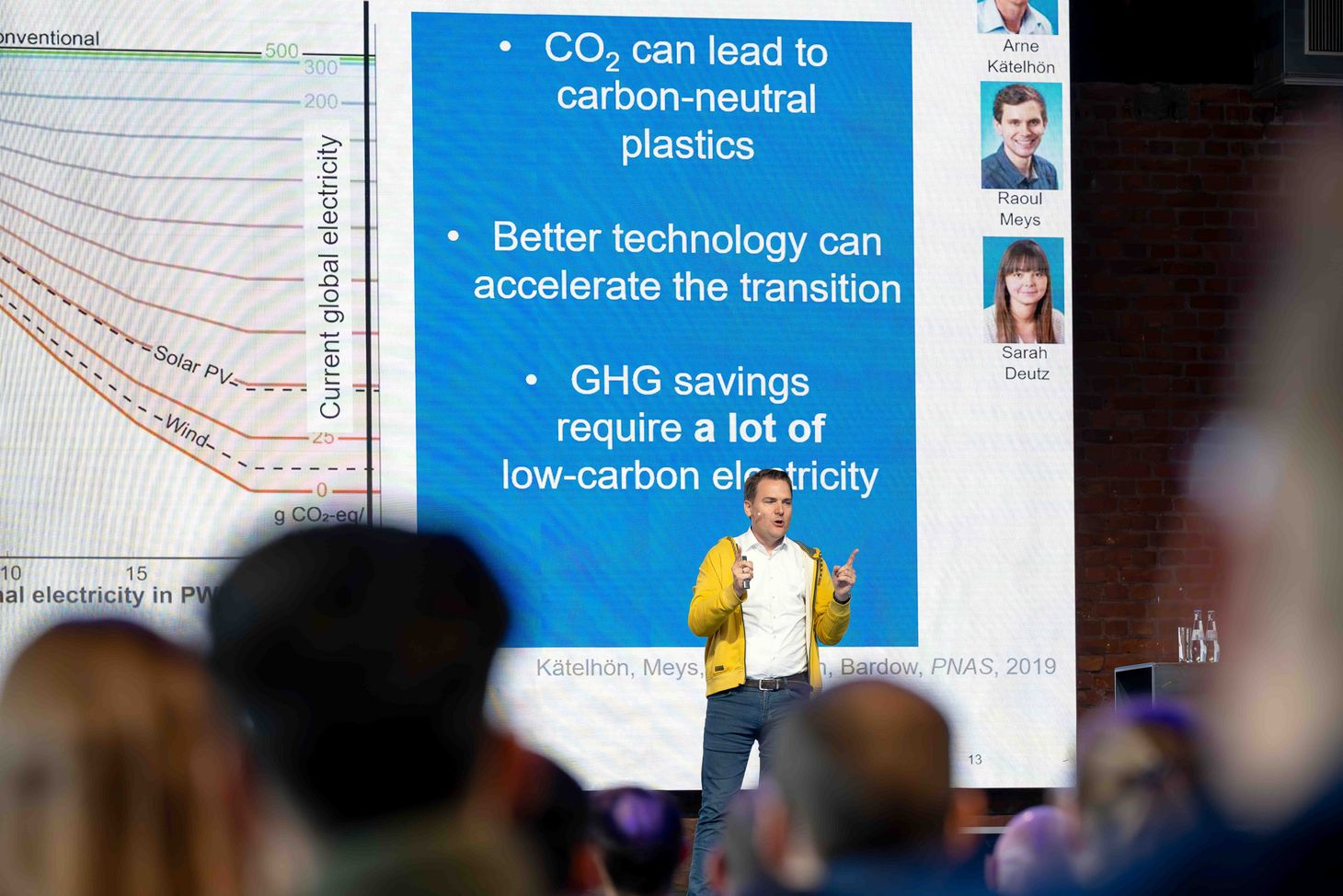
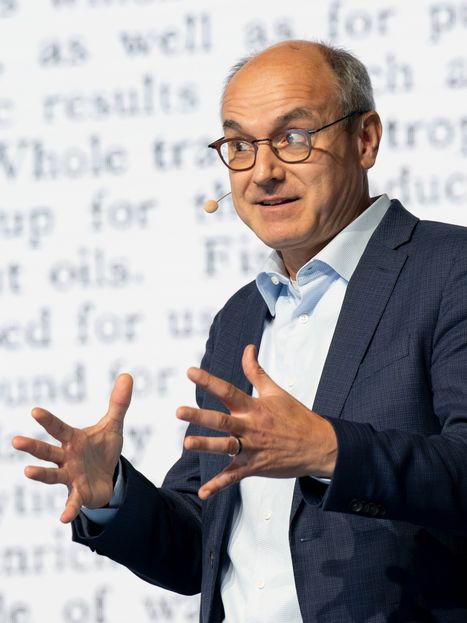
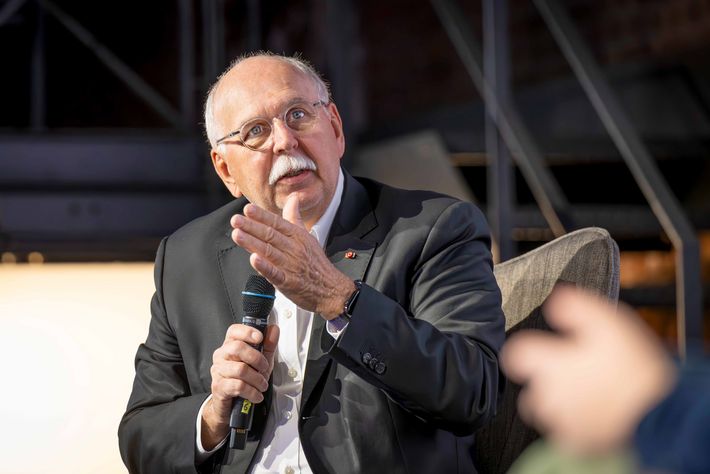
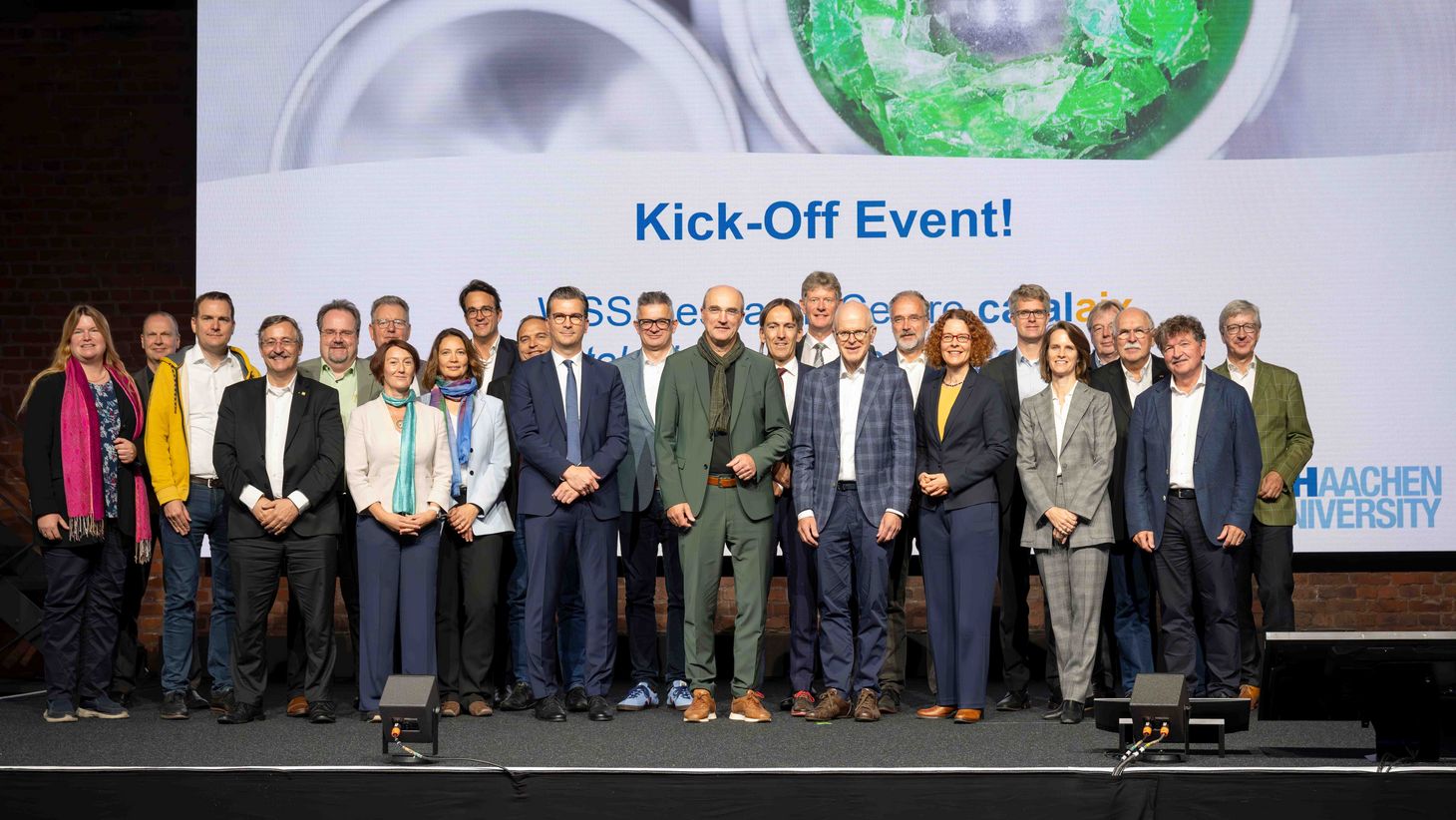