News
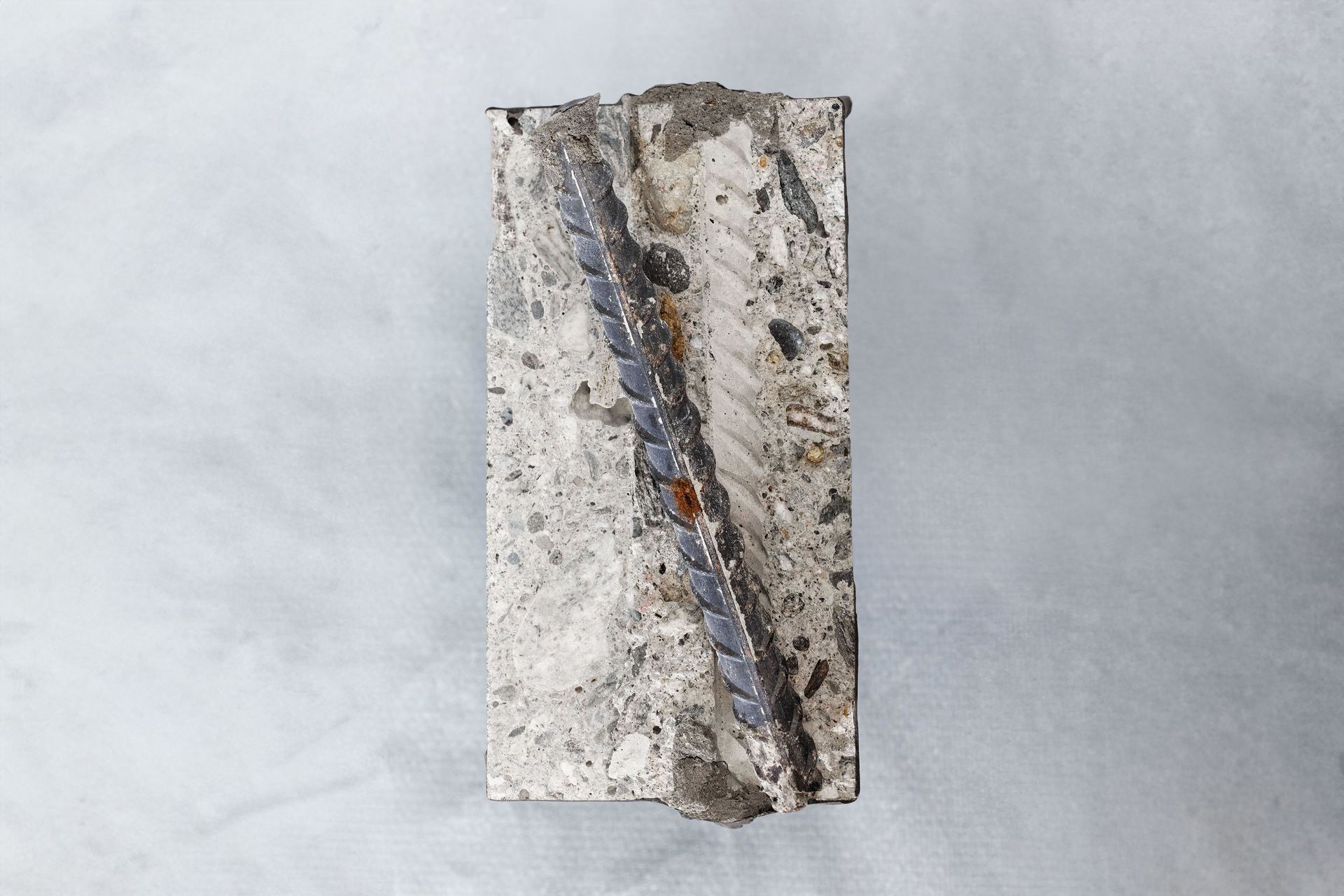
Reinforced concrete, corrosion and climate change
Concrete is the most widely used building material in the world. However, conventional methods of producing it release massive amounts of carbon dioxide into the atmosphere. What’s more, the firmly held conviction that high alkalinity alone protects concrete from corrosion often prevents more climate-friendly concrete structures from being built. Now, in a project recently awarded WSS funding, Ueli Angst, civil engineer and professor at ETH Zurich, is laying the groundwork for novel corrosion prevention.
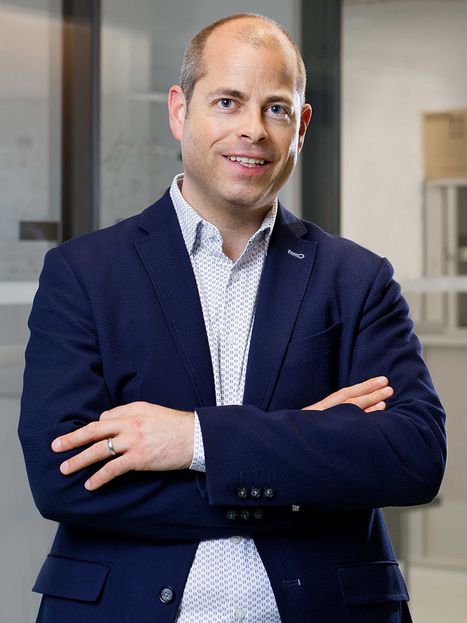
Ueli Angst, concrete is a massive success story. Across the globe, 600 gigatons of concrete—enough to build a total of ten Matterhorns—have already been used in construction projects. Why has this particular material become so widespread?
Concrete is relatively inexpensive, and its components—limestone, clay, sand and gravel—are found almost everywhere in the earth’s crust. That means it can be manufactured locally, eliminating long transport routes. Another advantage is that concrete can be used to create a multitude of forms. And, when reinforced with steel, concrete is incredibly strong and durable, making it ideal not only for constructing offices and residential buildings, but also major infrastructure projects like bridges and tunnels.
Why are traditional types of concrete still chosen over new, less environmentally detrimental kinds?
To this day, there’s a firmly held conviction that only highly alkaline concrete—or traditional types of concrete—can safely protect the embedded reinforcement steel, or rebar, from corrosion. This doctrine has rarely been questioned. But now, by conducting comprehensive research into corrosion processes in concrete and steel, we want to topple the old high-alkalinity dogma and pave the way for building more ecological, climate-neutral concrete structures. We’re convinced there are better options for preventing corrosion while nevertheless guaranteeing the longevity of a structure.
What makes you so certain that high alkalinity isn’t the best way to protect reinforced concrete from corrosion?
Three years ago, we analysed the data from nearly four hundred buildings in Switzerland, Finland and Japan, all of which were older structures. Due to exposure to carbon dioxide in the atmosphere, the concrete where the rebar is embedded was no longer alkaline. And yet, only five to ten percent of these buildings presented relevant corrosion problems. We interpret this as clear empirical evidence that protection from corrosion can be guaranteed in concrete that isn’t highly alkaline.
“We’re convinced that high alkalinity in concrete—bought at the price of massive CO2 emissions—isn’t the only way to protect against corrosion.”
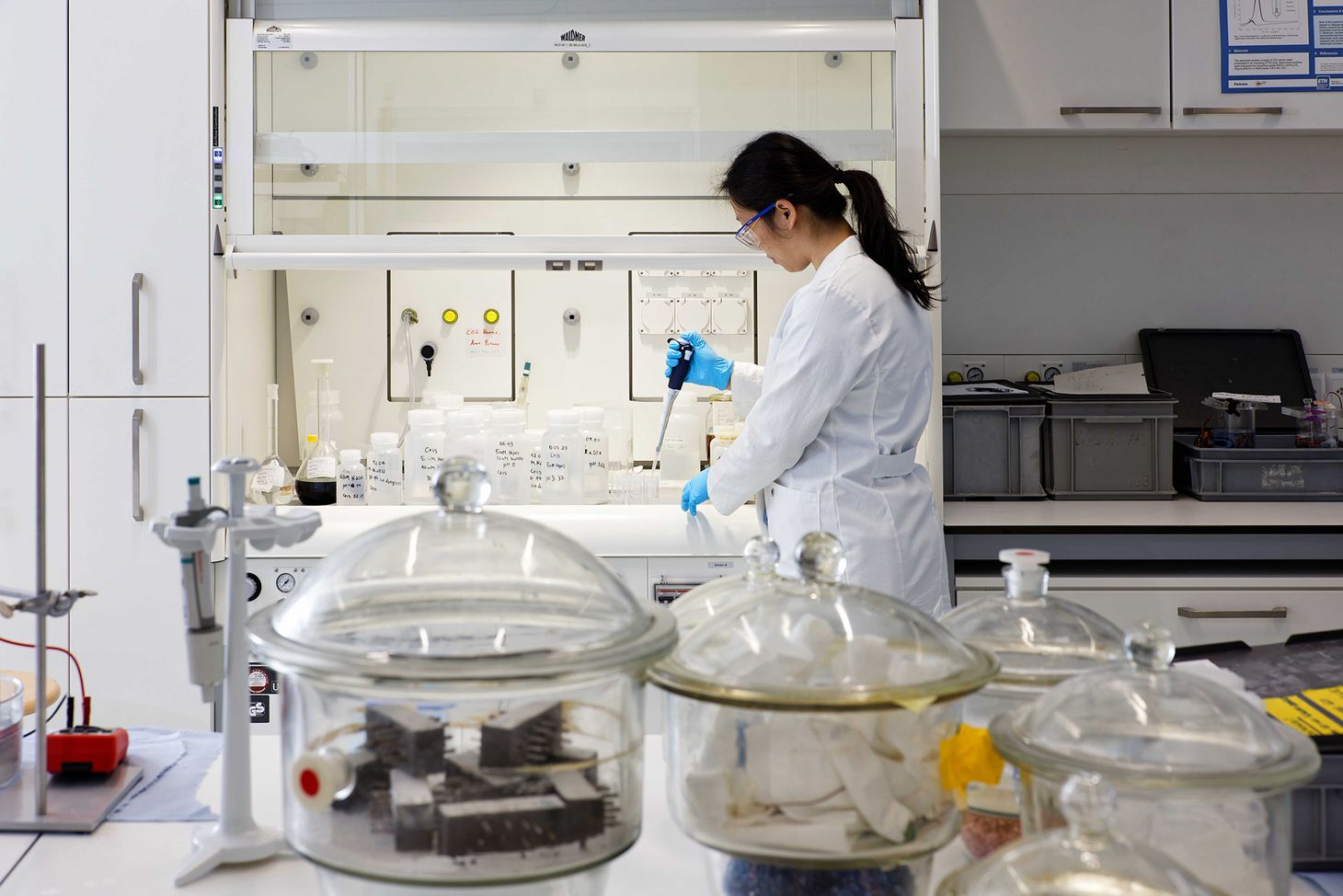
What factors trigger corrosion?
Humidity is a major cause. In certain conditions, high humidity alone can promote corrosion processes; but in our latitudes, it’s mainly rain or spray from the road that damages buildings.
Your aim is to initiate a paradigm shift in protecting reinforced concrete structures from corrosion. What do other specialists in the field think of your plans?
In the WSS project, we’re aiming to develop quantitative models that predict the corrosion risk in reinforced concrete under specific conditions
and also to identify which corrosion protection methods are best suited for a given situation. I’ve introduced our new approach to the scientific community at various events. For example, last September in Thailand, at the International Congress on the Chemistry of Cement—the world’s largest trade congress—I was one of the keynote speakers and had the opportunity to demonstrate how current practices in concrete manufacture conflict with climate protection and how we can change that. I’ve also presented this same view at other international conferences in North America and Europe. Overall, the echo has been very positive, and our ideas have been particularly well received in the cement and concrete industry.
Concrete is hard. How is it possible that moisture infiltrates deep enough to reach the reinforcement bars?
There are complex pore systems in concrete. Moisture travels through the pores relatively quickly—it’s sped up by capillary suction, much like in a sponge. And once water has penetrated the concrete, it takes from days up to weeks for it to evaporate again.
What happens to the concrete when moisture causes the rebar to rust?
At the start, the iron ions in the steel are simply dissolved in the water and don’t cause any damage. But over time, numerous chemical and electrochemical reactions are set in motion. For example, the iron ions can bond with hydroxide ions or with other ions in the pore solution. This can cause precipitates to form that are then deposited in the concrete’s pore system. And it doesn’t necessarily have to happen where the steel is—the dissolved ions can also diffuse in the concrete a few millimetres or even centimetres away from the reinforcement steel and first precipitate there. Actual damage to a concrete structure occurs when these processes cause cracks to form or when the steel corrodes to such an extent that it’s no longer functional. However, many aspects of what happens aren’t yet fully understood. That’s why we want to study the processes in detail.
“We’re studying corrosion processes in reinforced concrete in minute detail.”
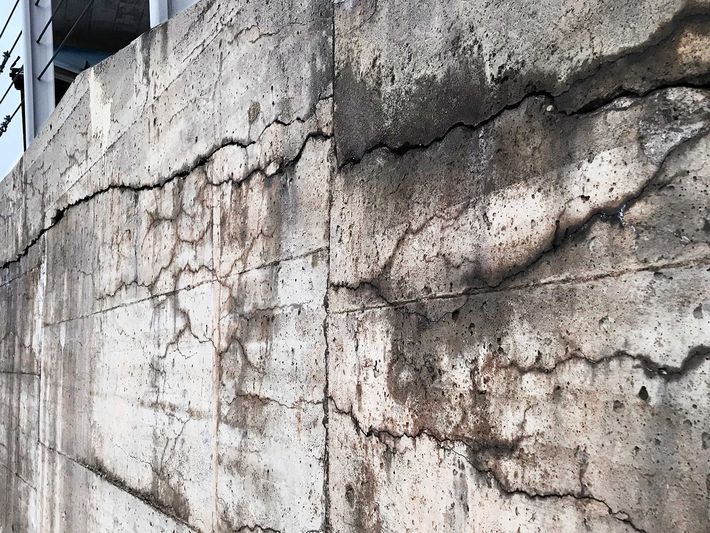
Concrete damages the environment
The gigatons of concrete produced across the globe generate massive CO2 emissions. Most of the greenhouse gas is released during calcination, a chemical reaction that occurs during the manufacture of traditional, high-alkaline concrete. During calcination, the binder material cement is admixed with water and aggregate materials such as sand and gravel. In this mixture, cement poses the greatest problem for the climate. Cement is made using limestone and raw materials like clay, which are fired in a furnace, where the massive heat breaks the limestone down into calcium oxide and CO2. Overall, calcination is responsible for sixty percent of the carbon dioxide emitted during concrete manufacturing. The remaining forty percent result from heating the furnace, transporting raw materials, and grinding the minerals and cement clinker.
What aspects of corrosion need to be understood for your work?
It’s crucial to know how far the iron ions “travel”. If they make it far into the concrete, the precipitates spread out more with the result that less pressure builds in the concrete than when the reactions occur closer to the reinforcement steel. In the latter case, local stresses arise quickly, potentially causing cracks to form.
What other aspects of corrosion are you and your team studying?
We want to know more about how the pore systems in different kinds of concrete behave. This includes how well water passes through, how much moisture reaches the steel, how quickly and under what conditions this occurs, how long water stays there, how soon corrosion sets in—and
how fast it develops. We also want to know when alternating between getting wet and drying, then getting wet and drying again causes corrosion damage. Because one thing is certain: if we want to use new types of low-alkaline concrete, we have to know how to manage moisture levels and the associated corrosion kinetics.
What parts of the process are particularly difficult to research?
Studying corrosion of metal inside a porous material is a highly complex undertaking. Up to now, the experimental means we have for observing corrosion processes in situ are limited, and they don’t provide an accurate picture of what actually happens. That’s why we’re developing innovative experimental methods for studying corrosion where it occurs.
Other problems arise due to large differences in spatial dimensions. Some corrosion occurs in the nano-range, others on a scale of centimetres or even metres, making it extremely challenging to create a digital model of a pore structure that both encompasses and brings all these differences together. But that’s precisely what we aim to do in the WSS project: connect all the various dimensions.
How will you go about doing that?
Because corrosion processes are multifaceted and highly dynamic, computer simulations are ideal for conducting a systematic analysis. But they also require a lot of computing power and are expensive—just one reason why the grant from the Werner Siemens Foundation is so important for our project.
What practical benefits do computer simulations have?
We’re looking to develop computer simulations that are viable for any and every concrete mix—because, in future, hundreds of different concrete types will be developed and used in construction projects. Ideally, our method will simulate rebar corrosion in these different kinds of concrete across all spatial dimensions. In addition, the models should be designed to incorporate meteorological data like the maximum duration of precipitation in a given country. Our vision is to deliver such accurate forecasts of the long-term behaviours of reinforced concrete in various climates that they’ll be of direct use for planning and maintaining infrastructure.
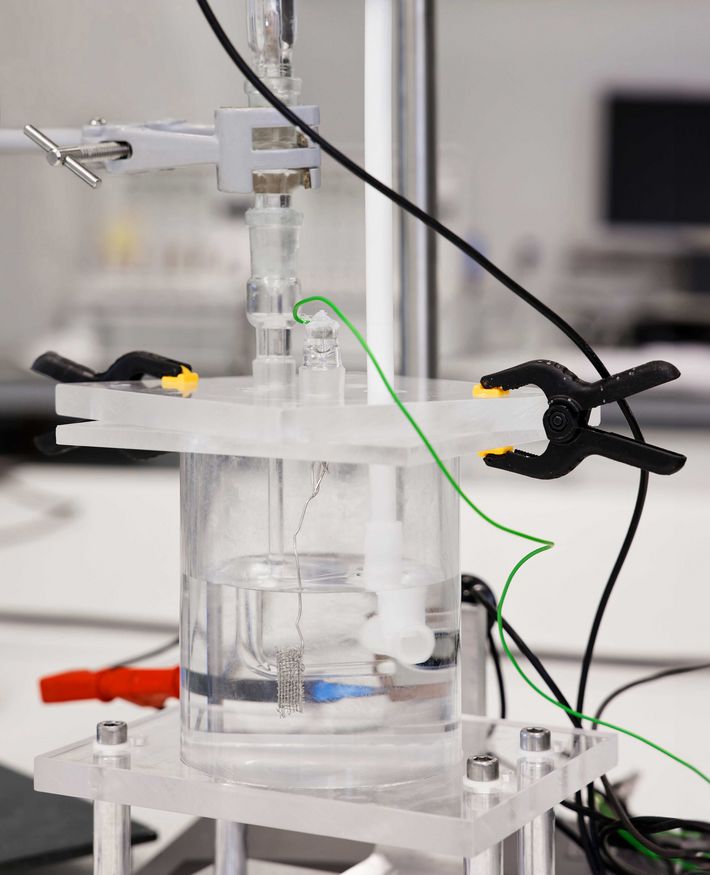
Do you already have ideas about corrosion protection in structures made of low-alkaline concrete?
Yes. Instead of focusing on managing alkalinity in concrete for the next hundred years—as is the current practice—we’re looking to regulate moisture levels. Up to now, test methods have been based on analysing how quickly alkalinity is lost. I think it’s wiser to study and manage the properties of moisture transport in new concrete.
How can you manage moisture in concrete?
Moisture levels depend not only on the concrete itself, but also to a large measure on how exposed a structure is. In places with low average rainfall, even relatively porous concrete can offer enough protection from corrosion. In regions with heavy precipitation, by contrast, denser concrete, more reinforcement, even an additional coating may prove necessary. In order to select the correct parameters during the planning stage, we need to develop numerical models and lab test methods based on the relevant variables and processes.
Aside from adding a coating, are there any other ideas for protecting concrete from moisture?
Other than surface treatments and directly influencing the microstructure of the cement phases via concrete technology, there are many interesting alternatives and approaches. One idea is to add filler materials like cellulose fibres to the concrete mix. In the timber industry, massive amounts of cellulose accumulate, and it’s generally disposed of as waste. But if it were mixed into concrete, it could help regulate moisture. Another approach is introducing living organisms like bacteria or fungus-like organisms, that accelerate calcium carbonate precipitation and thus seal the pore system. Enzymes are also another promising possibility in this context.
“We want to use sensors embedded in concrete to monitor a structure’s health.”
Using microorganisms to inhibit corrosion—it sounds futuristic!
Yes, and there are also many microorganisms that accelerate CO2 storage We could apply this basic principle for use in concrete. Currently, a PhD
student in our team is working on this aspect.
And how can you prevent corrosion in the case of already existing reinforced concrete structures?
Our idea is to use sensors that are embedded at various depths in the concrete to monitor the structure’s health. The sensors function as an early warning system and are designed to emit a signal should problems occur—too much water seeping into the concrete, for example. This knowledge equips us with the means to adopt measures to offset the corrosion. The ETH spin-off DuraMon, which I co-founded three years ago, manufactures these kinds of sensors.
You mentioned that concrete could even function as a carbon sink. How is that possible?
A law of nature says that all chemical compounds tend towards thermodynamic stability, a state in which a compound is in chemical equilibrium with its environment. In the case of concrete, the carbon dioxide that splits off at temperatures of over 1400 degrees Celsius during conventional concrete manufacture wants to bond again with calcium hydroxide to form limestone, the starting material.
How does that relate to storing carbon dioxide in concrete?
Already today, small amounts of CO2 from the air diffuse continuously in concrete structures, where they undergo chemical reactions. But this process is extremely slow and it would take millennia for concrete to return to a material that’s similar to its original stage. Once we can manage corrosion, however, we can harness this natural process and use innovative technologies to store carbon dioxide in traditional kinds of concrete.