Aktuell

Ausgeklügelte Implantate
Der 3D-Druck von patientenspezifischen Implantaten ist einer der Stützpfeiler des MIRACLE-II-Projekts an der Universität Basel. Nun unternehmen die Forschenden erste Schritte, um sogar Implantate zu drucken, die sich im Körper abbauen. Sie könnten Folgeoperationen überflüssig machen.
Schonende, minimalinvasive und hochpräzise Knochenoperationen – daran arbeiten die Forschenden des MIRACLE-II-Projekts an der Universität und am Universitätsspital Basel. Unterstützt von der Werner Siemens-Stiftung entwickeln sie dazu ein robotergesteuertes System, das Knochen mittels Laser schneidet. Und im spitaleigenen 3D-Druck-Labor entstehen Implantate, die genau in den vorgeschnittenen Knochen passen.
Im vergangenen Jahr setzte das Team um Professor Florian Thieringer, Chefarzt für Mund-, Kiefer- und Gesichtschirurgie und Leiter des 3D-Druck-Labors am Universitätsspital Basel, erstmals in Europa einem Patienten eine Schädelplatte ein, die am Spital designt und gedruckt worden war. Um die Vorgaben der Verordnung für Medizinprodukte einzuhalten, wurde das Start-Up PoC-APP gegründet, welches das Spital regulatorisch begleitet und dieses Wissen auch an weitere Spitäler vermittelt. Solche selbst gedruckten Implantate bestehen aus Kunststoffen oder Knochenersatzsubstanzen. Zukünftig aber könnten für bestimmte Implantate vielleicht auch Materialien benutzt werden, deren Bestandteile vom Körper vollständig abgebaut und durch körpereigene Gewebe ersetzt werden.
Für eine kürzlich im Fachmagazin «3D Printing in Medicine» erschienene Studie (*) untersuchte ein Team um Thieringer die Machbarkeit von verschiedenen patientenspezifischen Implantaten aus einem solchen bioresorbierbaren Material. Bei dem Material handelte es sich um ein Milchsäure-Kalziumphosphat-Gemisch, das bereits für die Verwendung am Menschen zugelassen ist.
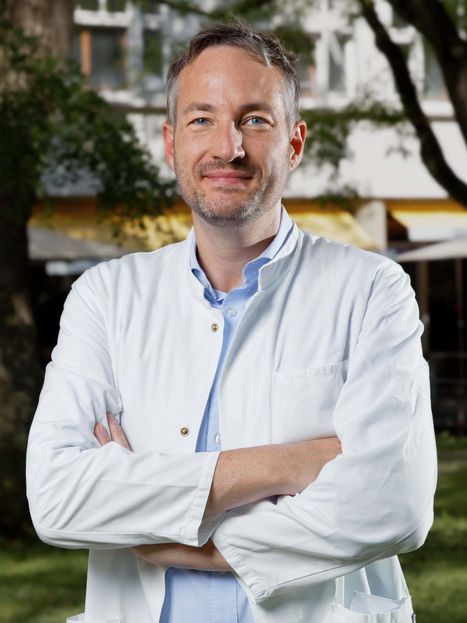
Platten, Meshes, Knochengerüste
Die Vorgehensweise war grundsätzlich dieselbe, welche die Forschenden auch für den 3D-Druck von bisher eingesetzten Implantaten anwenden: Zuerst erstellten sie Computer-Tomografie-Bilder des geschädigten Körperteils. Anhand der Bilder erzeugten sie eine digitale Vorlage für ein patientenspezifisches Implantat. Das 3D-Implantat druckten die Forschenden mit einem speziellen 3D-Drucker der Firma Arburg. In einem Ultraschallreiniger wurde das so hergestellte Implantat von winzigen Verunreinigungen befreit und schliesslich sterilisiert.
Die Forschenden zeigten, dass sich auf diese Weise eine ganze Reihe unterschiedliche bioresorbierbare Implantate herstellen lassen: Platten, mit denen sich Knochenbruchstücke aneinander fixieren lassen; verschiedene Implantate für Augenhöhlenboden-Frakturen; sogenannte Meshes, eine Art Netze, welche das Nachwachsen von Kieferknochen erleichtern; und Knochengerüste, die von einer Vielzahl von Poren durchzogen sind.
Noch werden diese vom Körper abbaubaren 3D-Implantate nicht im Patienten eingesetzt. «Doch das ist der nächste Schritt», sagt Florian Thieringer. «Wir sind dabei, die Prozesse so zu validieren, dass wir sie in der Klinik einsetzen können.» Es ist derselbe Prozess, die Forschenden bereits für durchlaufen mussten, um eine Zulassung zu erhalten für den 3D-Druck und den klinischen Einsatz des Kunststoffs Polyetheretherketon (PEEK), aus dem das letztes Jahr erstmals benutzte Schädeldachimplantat besteht.
Ein Eingriff weniger
Dass bioresorbierbare Materialien sich mit der Zeit im Körper auflösen, ist ein grosser Vorteil für bestimmte Anwendungen. «Die Idee ist es, dass sie mit der Zeit durch körpereigene Gewebe ersetzt werden», sagt Florian Thieringer. Das bedeutet zum Beispiel, dass sie einen Folgeeingriff überflüssig machen, der je nachdem notwendig ist für die Entfernung eines nicht abbaubaren Implantats.
Ein konkretes Anwendungsgebiet sei der Knochenaufbau vor einer Zahnimplantation, erzählt Thieringer. Wenn ein Mensch mehrere Zähne verloren hat, kann es sein, dass der unterliegende Kieferknochen langsam verschwindet. Dann muss der Chirurg zuerst einen Knochenaufbau machen, um ein Zahnimplantat einsetzen zu können. «Wenn wir dafür Materialien wie Titangitterchen verwenden, die wieder entfernt werden müssen, braucht es stets einen Zusatzeingriff – das ist belastend für den Patienten», sagt Thieringer.
Eine weitere Einsatzmöglichkeit ist die Operation von Kindern mit einer Fehlbildung, etwa mit Lippen-Kiefer-Gaumen-Spalten oder Schädeldeformitäten. «In solchen Fällen wird ein Knochenaufbau gemacht im Spaltbereich oder der Schädelknochen ummodelliert. Aber Kinder wachsen – für sie sind starre Materialien nicht geeignet, denn diese verändern das Wachstum», sagt Thieringer. Selbstresorbierbare Materialien hingegen würden das Wachstum nicht beeinflussen.
Mehrwert ohne Mehrkosten?
Bevor die auflösbaren Materialien aus dem 3D-Drucker zum Einsatz kommen, gilt es eine ganze Reihe von Herausforderungen zu meistern. Noch ist zum Beispiel nicht klar, welche Materialien für welche Zwecke besonders gut geeignet sind. Ein interessantes Material sei Magnesium, sagt Thieringer. «Damit gibt es erste Anwendungen und laufende Projekte mit vorsichtigen Erfolgen.» Aber klinische Studien im menschlichen Körper müssten beispielsweise das Resorptionsverhalten des Materials untersuchen: Wenn Magnesium sich auflöst, entsteht Wasserstoff. «Das führt zu Gasbildung um Implantate herum, was allenfalls negative Effekte auf die Knochenheilung haben könnte.»
Die Wahl des geeigneten Materials, dessen Verarbeitung und biologische Verträglichkeit sind also grosse Hürden auf dem Weg zum Einsatz von resorbierbaren Materialien in der Chirurgie. Andere sind Technologien und Produktionsprozesse. Und eine weitere wichtige Herausforderung betreffe die Regulatorik, sagt Thieringer: «Von der Bildgebung und Planung über die Herstellung bis zur Sterilisierung und dem Einbringen in den Patienten muss die ganze Behandlungskette validiert und zugelassen sein.» Nicht zu vergessen die Wirtschaftlichkeit: «Wir müssen einen Mehrwert für unsere Patienten schaffen, ohne wesentliche Mehrkosten zu generieren.»
Thieringer ist überzeugt, dass der Einsatz von neuen, sich im Körper auflösenden Materialien Zukunft hat. Und nicht nur er: Kürzlich hat sein 3D-Druck-Labor einen neuen, kleiderschrankgrossen 3D-Drucker geliefert bekommen. «Die Firma Arburg war so überzeugt von unserer Forschung, dass sie uns das Flagship unter ihren 3D-Druckern zur Verfügung stellt», erzählt Thieringer. Damit lassen sich mehrere Komponenten gleichzeitig drucken – zum Beispiel ein wasserlösliches Stützmaterial und ein Knochenersatzmaterial. Beste Voraussetzungen also, um den 3D-Druck in der Medizin weiter voranzutreiben.
> * Link zur Studie
