
A second life for scrap metal
Cars, tools, household appliances: many of the most common and useful tools of daily life are made of metal. Recycling them at the end of their life cycle requires melting the metal parts down in an energy-intensive process. At TUD Dresden University of Technology, a project to develop a low-energy upcycling method has recently been awarded funding from the Werner Siemens Foundation.
Metal is a key building block in the global economy. According to the World Steel Association, roughly 1.9 billion metric tons of crude steel were produced worldwide in 2022—in addition to the millions of metric tons of aluminium and copper. These incomprehensibly vast quantities are cast, rolled, forged, milled and welded into the many different metal qualities and components used in the manufacture of vehicles, machines, bridges, pipes, tools and household appliances.
At the end of their life cycle, most of these valuable metal parts are melted down and processed into new parts. To be sure, current recycling methods save both resources and energy when compared to mining, extracting and primary production; however, they still consume massive amounts of energy. “Roughly ninety percent of the energy involved in the manufacture of a metal component is used for melting and rolling,” says Alexander Brosius, Chair of Forming and Machining Processes at TUD Dresden University of Technology.
Doing away with melting
Alexander Brosius is working with Andrés Fabián Lasagni, Chair of Laser-based Manufacturing at TUD, to make reusing and recycling metal components more sustainable. Their project—“2nd Life Metal Components”—aims to bypass the melting process entirely. Instead, they want to directly cut scrap metal parts, press the pieces into flat sheets, weld them together again and mould them into new forms. The Werner Siemens Foundation (WSS) is financing the innovative research project with a total of thirteen million euros over the next eight years.
The project’s novel approach is based on combining several different steel or aluminium parts into a new workpiece. No easy task, as Andrés Fabián Lasagni says: “The scrap metal we want to use comes in very different forms, degrees of thickness, strengths and qualities.” In today’s practice, it’s the melting process that reliably creates a uniform product for the subsequent metalworking and formation processes.
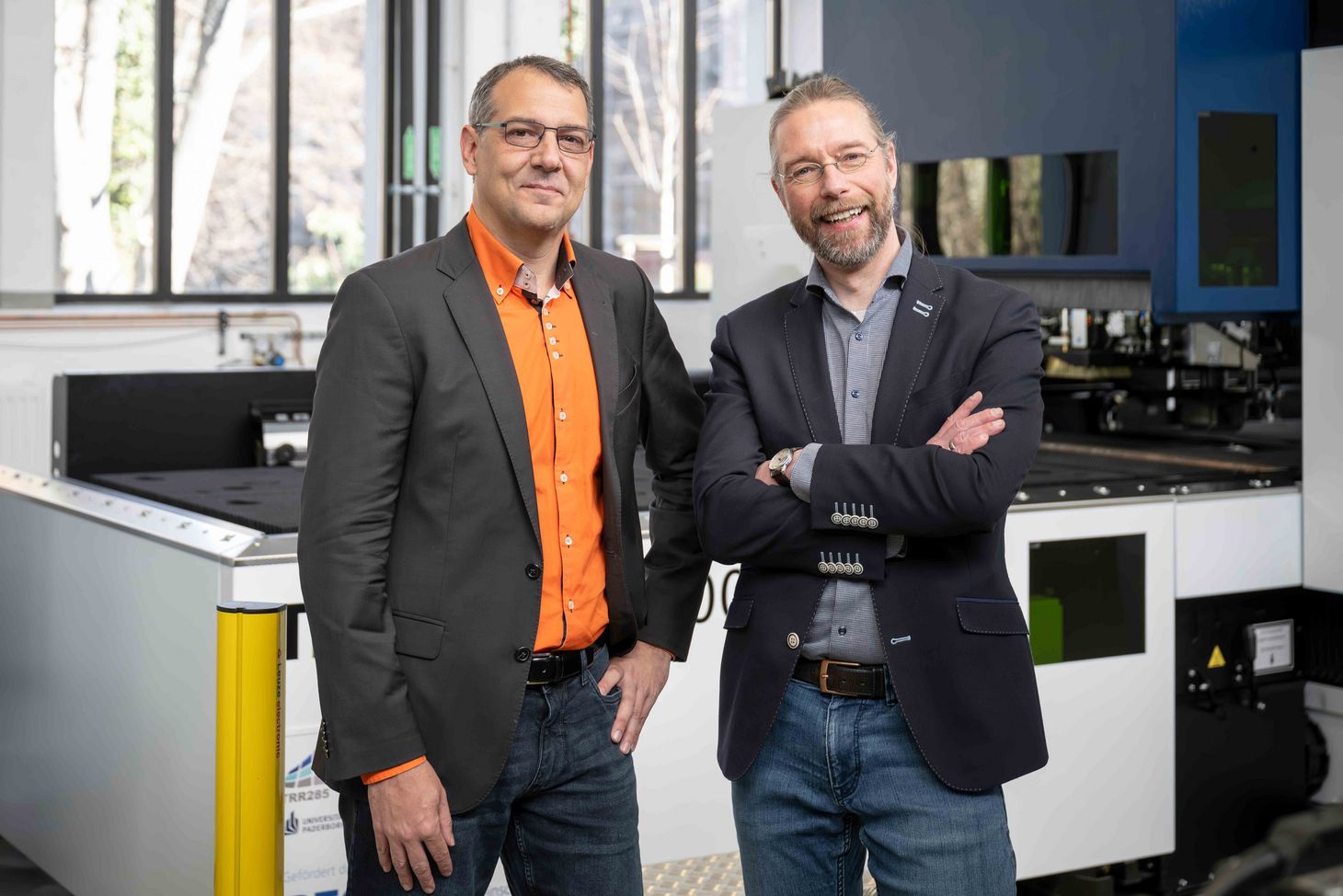
Scrap metal puzzle
The researchers have designed an entirely new process chain for their envisioned upcycling method that functions without melting. First, the supplied and available scrap metal is sorted and, when necessary, cleaned and stripped; afterwards the geometry, thickness and chemical composition of the workpieces are recorded. Only then does actual processing begin. Using laser cutting technology, curved, three-dimensional components such as car doors or metal tubs are cut apart and flattened. “It’s important to cut at the right places to prevent creases and cracks from forming when the metal is pressed into a flat sheet,” Alexander Brosius explains.
The mechanical properties of the new two-dimensional sheet metal are then characterised more precisely, without destroying the materials in the process. Information about a metal’s strength, microstructure and surface structure is key for knowing how—and for what purposes—the sheet metal can be further processed. Indeed, the investigation of properties and the development of methods for quickly, precisely and reliably identifying them at any stage of the process are integral aspects of the project.
The next step is a little like putting a puzzle together. Parts suitable for the desired workpiece are selected, assembled and welded together. And now, the technology that makes the entire project possible comes into play: “macrostructured deep drawing”. Deep drawing is one of the most widely used processes in sheet metal forming. The sheet metal, or “blank”, is clamped between what are known as the “blank holder” and the “die”; the metal is then bent, stretched and formed into a hollow body such as a tub, a sheath or a pot.
Flexible, robust process
Conventional deep drawing methods require large quantities of lubricant additives as well as precision placement of the blank. If, however, the blank’s thickness is uneven, only the wider sections will be clamped, which promotes the formation of cracks and creases in the workpiece. The macrostructured deep drawing process designed by Alexander Brosius and his team avoids this problem. Rather than clamping the blank flush between the blank holder and die, a mount with rotating balls is used. In this setup, balls on the blank holder and the die are offset so that the blank is only ever in contact with the upper or lower side—the blank holder or the die. “This makes it possible to work with sheet metal of uneven thickness,” Brosius says. “The manufacturing process becomes much more flexible and robust.”
However, the new, no-melt process has a drawback. The resulting metal components are less uniform than conventionally manufactured components. “They don’t look as smooth. Their thickness isn’t consistent and the seam welding is visible,” Brosius explains. What’s more, in extreme cases, some components are made of dozens of individual pieces of steel or aluminium, making them unsuitable for the painted and polished exteriors of cars, for instance. “But they’re absolutely viable for use as structural supports, where stability, not appearance, is the decisive factor.”
A central part of the project focuses on improving the properties of reused metal parts. This so-called “laser-based surface functionalisation” is the speciality of Andrés Fabián Lasagni, whose work includes developing methods to render metals and other materials water-, dirt- and bacteria-repellent. This is done by using a laser to produce minuscule structures measuring just micro- or nanometres into a metal’s surface. “For example, we can boost corrosion protection in metal components or—for the food industry—ensure that surfaces remain germ-free,” Lasagni explains.
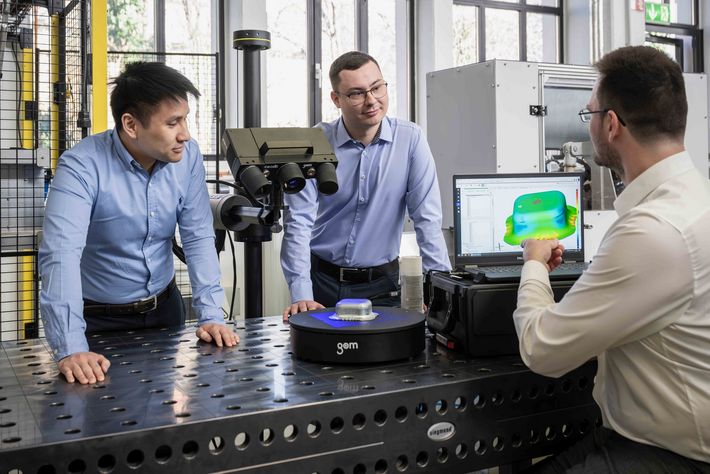
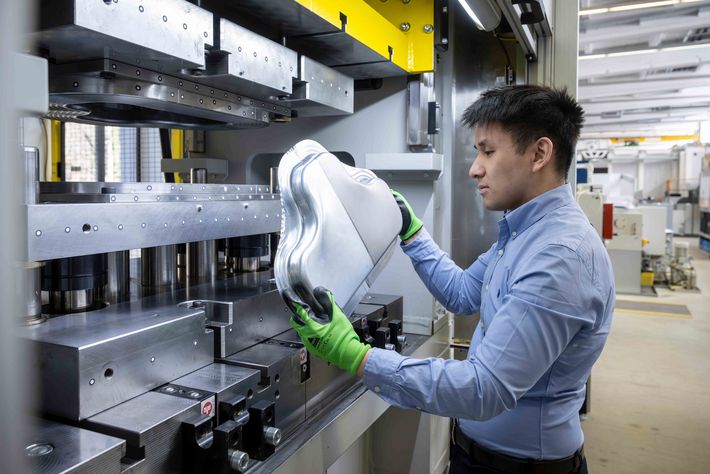
“I was a Porsche in my last life”
This refinement technique is what enables the Dresden project to go beyond simply recycling metal. “We’ll be fabricating metal components that have different, improved functionalities over the base material,” Lasagni says. Both project leaders are confident that the improvements in quality will more than compensate for the visual disadvantage caused by not melting down the metal.
Especially as they have another ace up their sleeve. Laser techniques also make it possible to label or otherwise mark the metal parts. A groove just a few micrometres deep is enough to protect the engraved information from mechanical abrasion—and only a special software program can decode the markings. Practical details such as the composition, properties or origin of a metal part might be encoded, but more whimsical particulars are also conceivable. For instance, a component might contain a declaration about its previous “life”. For example: “I used to be a rubbish bin.” Or: “I was a Porsche in my last life.”
With all the scrap metal on the market, the researchers must first decide what kind they want to focus on. Lasagni and Brosius say detailed answers will emerge only as the project progresses. What’s already clear, however, is that their initial priority will be on larger, simpler forms, then increasingly on smaller, more complex components and combinations. “Our first step is to use our method for fabricating the metal components. Then we’ll progressively make improvements,” Alexander Brosius says.
Model factory and classification app
At the same time, a second obstacle has also arisen at the outset of the project. If the new techniques are to become standard practice in industry, the researchers need to deliver more than laboratory evidence. “Businesses want guarantees that our process chains are viable for large-scale production,” Brosius says. To offer these assurances, the researchers are planning a model factory—a production line that uses workpiece examples to show how new components are manufactured from specific kinds of scrap metal in an automated, step-by-step procedure. The process chain is relatively long, Andrés Fabián Lasagni says, adding that the integration and interaction of the individual steps—the planning process itself—is one of the project’s biggest challenges.
A second pathway for boosting their method’s chances on the market is the development of a classification app. “Put simply, the idea is that someone can go to the scrapyard and use their phone to take pictures of the scrap metal parts they’re interested in,” Alexander Brosius explains. “The app then calculates what new components could be made from the items.”
Both researchers agree that these—and other—clever methods and strategies will be needed to get their project off the ground, especially because the metal upcycling processes they’re developing represent an existential challenge to current production practices. If, however, they succeed in bringing their approach to industrial application, they’ll have made a major contribution towards transforming one of the most energy-intensive production lines into a more sustainable industry.
Facts and figures
Funding from the Werner Siemens Foundation
13 million euros
Project duration
2025 to 2032
Project leaders
Prof. Dr.-Ing. Alexander Brosius, Chair of Forming and Machining Processes at TUD Dresden University of Technology
Prof. Dr.-Ing. Andrés Fabián Lasagni, Chair of Laser-based Manufacturing at TUD Dresden University of Technology
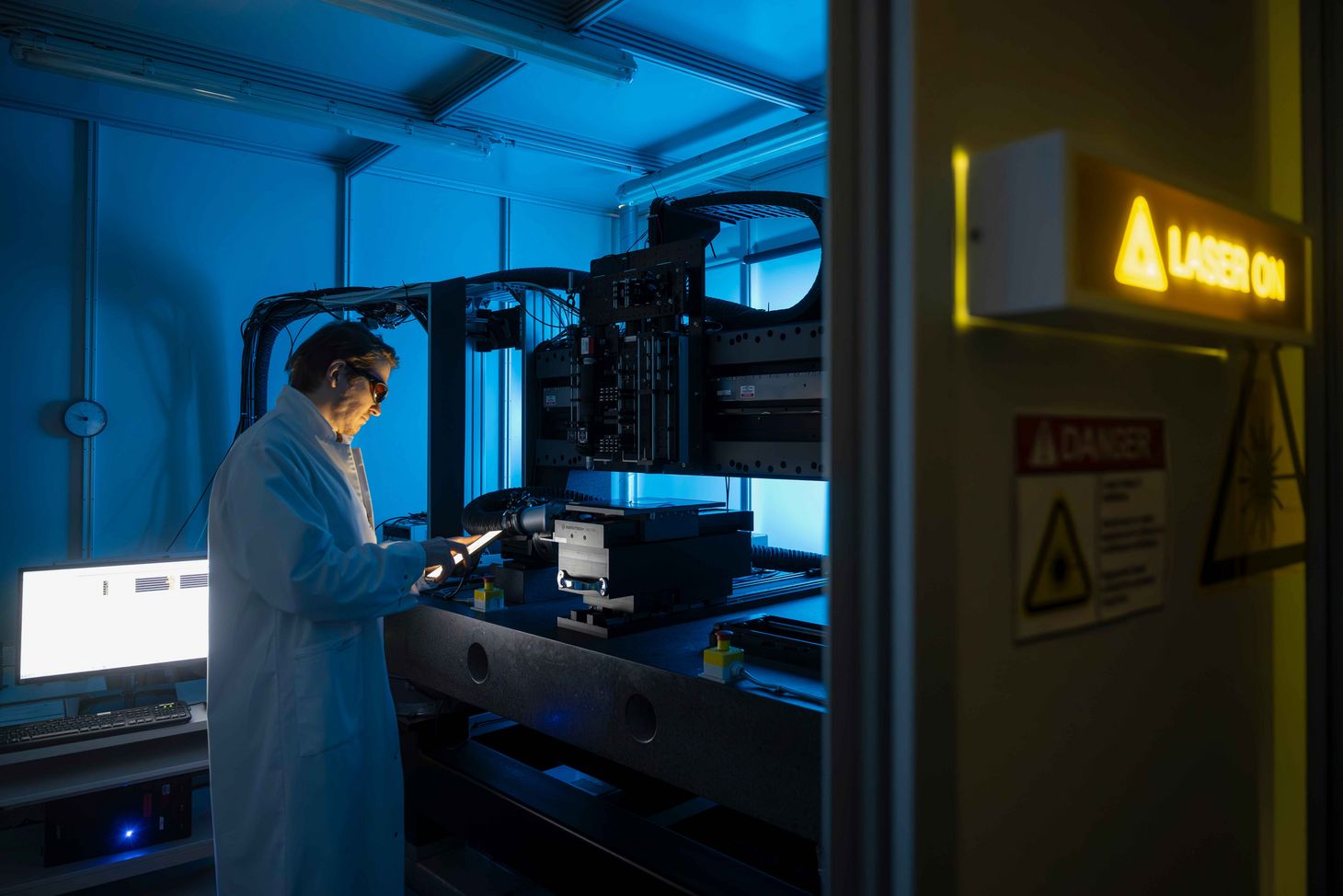