
Ein zweites Leben für Metallbauteile
Autos, Werkzeuge, Haushaltgeräte: Viele unserer wichtigsten und nützlichsten Produkte bestehen aus Metall. Um sie zu rezyklieren, werden Metallbauteile heute eingeschmolzen. Ein neu von der Werner Siemens-Stiftung unterstütztes Projekt an der Technischen Universität Dresden will diesen energieintensiven Schritt mit einem cleveren Ansatz umgehen.
Metalle sind die Bausteine der Weltwirtschaft. Rund 1,9 Milliarden Tonnen Rohstahl wurden im Jahr 2022 laut dem Welt-Branchenverband der Stahlindustrie erzeugt. Dazu kommen Millionen Tonnen weitere Metalle wie Aluminium oder Kupfer. Diese unvorstellbaren Mengen werden gegossen, gewalzt, geschmiedet, gefräst und geschweisst. So entstehen unterschiedlichste Metall-Qualitäten und -Bauteile, die sich zur Herstellung von Fahrzeugen, Maschinen, Brücken, Rohren, Werkzeugen oder Haushaltgeräten eignen.
Ein grosser Teil dieser wertvollen Werkstoffe wird am Ende ihrer Lebensdauer eingeschmolzen und zu neuen Bauteilen verarbeitet. Das spart zwar – verglichen mit dem Rohstoffabbau und der Neu-Produktion – Ressourcen und Energie. Aber es bleibt ein enorm energieaufwändiger Prozess. «Ungefähr 90 Prozent der Energie zur Herstellung eines Metallbauteils werden für das Einschmelzen und Walzen benötigt», sagt Alexander Brosius, Professor für formgebende Fertigungsverfahren an der Technischen Universität (TU) Dresden.
Einschmelzen unnötig machen
Gemeinsam mit Andrés Fabián Lasagni, Professor für laserbasierte Fertigung an der TU Dresden, will Brosius die Wieder- und Weiterverwendung von Metallbauteilen nachhaltiger machen. Mit einem neuen Projekt namens «2nd Life Metal Components» wollen sie den Einschmelzprozess umgehen – stattdessen werden Metallteile direkt aufgetrennt, zu einem flachen Blech gepresst, wieder zusammengeschweisst und in neue Formen gebracht. Die Werner Siemens-Stiftung (WSS) unterstützt das innovative Vorhaben in den kommenden acht Jahren mit insgesamt 13 Millionen Euro.
Der neuartige Ansatz beruht darauf, jeweils mehrere unterschiedliche Stahl- oder Aluminiumbauteile zu einem neuen zusammenzufügen. Eine Herausforderung, wie Andrés Fabián Lasagni sagt: «Die alten Metallstücke, die wir verwenden wollen, kommen in ganz unterschiedlichen Formen, Dicken, Festigkeiten und Qualitäten daher.» Bei den heutigen Prozessen sorgt das Einschmelzen dafür, dass stets ein einheitliches Ausgangsprodukt für die nachfolgende Blechbearbeitung entsteht.
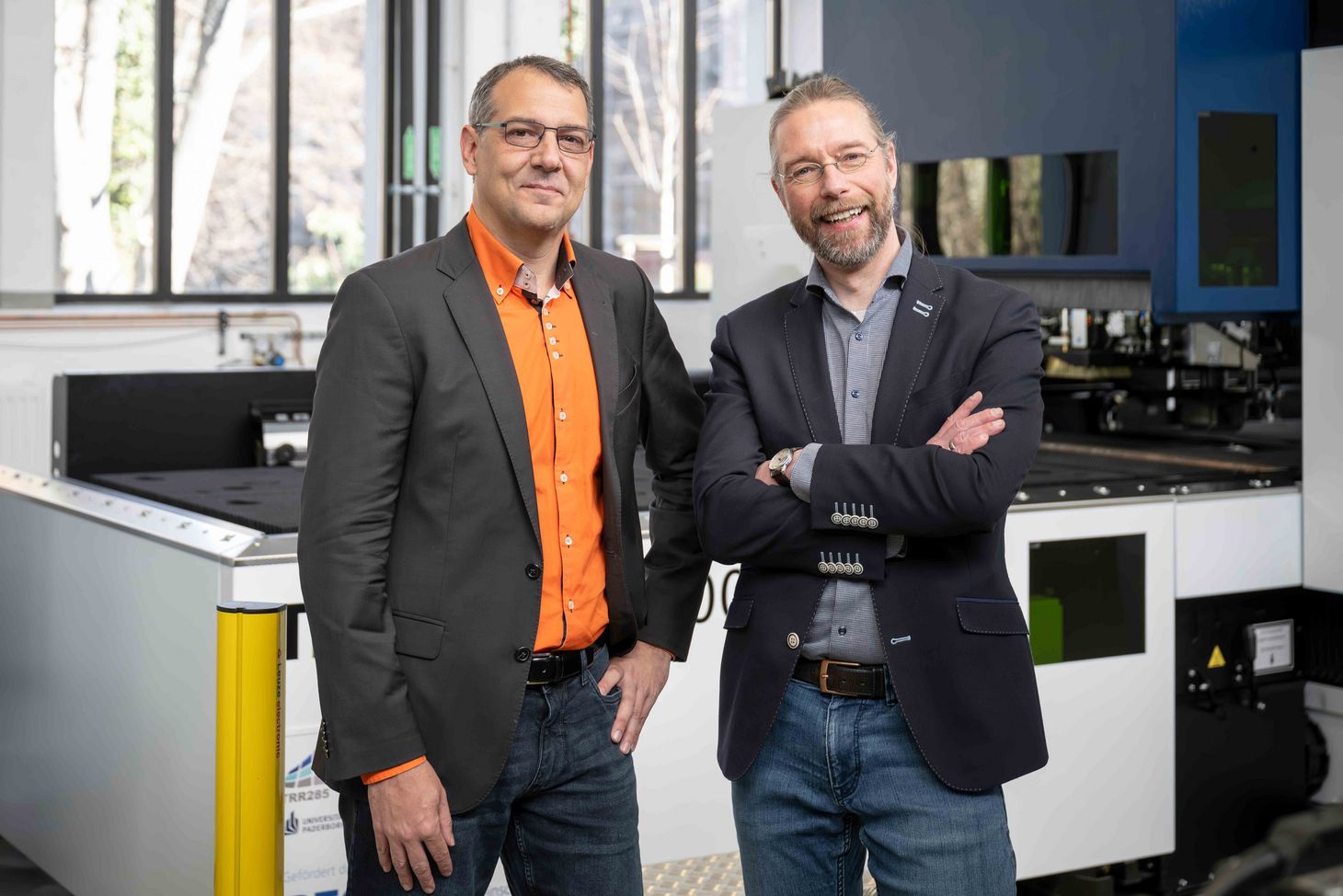
Altblech-Puzzle
Für das geplante Upcycling ohne Einschmelzen haben die Forscher ganz neue Prozessketten entworfen: Als erstes werden die angelieferten und zur Verfügung stehenden Bauteile sortiert, allenfalls gereinigt oder entlackt und die Geometrie, die Blechdicke und die chemische Zusammensetzung erfasst. Danach beginnt die eigentliche Verarbeitung: Gebogene, dreidimensionale Bauteile – zum Beispiel eine Autotür oder eine Spülwanne – werden per Laserschnitttechnik aufgetrennt und flachgedrückt. «Schnitte an den richtigen Stellen sind nötig, damit beim Pressen zum flachen Blech keine Falten oder Risse entstehen», erklärt Alexander Brosius.
Die mechanischen Eigenschaften der entstehenden platten, zweidimensionalen Blechteile werden nun genauer charakterisiert – ohne sie dabei zu zerstören: Die Festigkeit, die Mikrostruktur und die Oberflächenstruktur sind entscheidend dafür, wie und wozu ein Blechteil weiterverarbeitet werden kann. Die Erforschung und Entwicklung von Methoden, um solche Eigenschaften schnell, genau und in dem gesamten Prozessablauf zuverlässig zu ermitteln, sind wichtige Teile des Projekts.
Nun folgt ein Schritt, der an das Zusammensetzen eines Puzzles erinnert: Die passenden Teile für ein geplantes Werkstück werden ausgewählt, zusammengefügt und neu verschweisst. Danach kommt jene Technik zum Einsatz, die das gesamte Projekt überhaupt ermöglicht: das sogenannte «makrostrukturierte Tiefziehen». Tiefziehen ist eines der wichtigsten Umformverfahren in der Umformtechnik. Die Blechplatine wird zwischen einer Halterung, dem sogenannten Niederhalter, und einer Matrize eingespannt und danach durch Strecken und Stauchen in einen Hohlkörper – zum Beispiel eine Wanne, eine Hülse oder einen Topf – verwandelt.
Flexibles, robustes Verfahren
Herkömmliche Tiefziehverfahren benötigen grosse Mengen von Schmiermitteln und genaue Anpassungen an das zu bearbeitende Blechstück. Spannt man beispielsweise ein Blechstück ein, das aus unterschiedlichen Dicken besteht, werden nur dickere Partien eingeklemmt, was leicht zu Rissen und Falten führt. Das vom Team um Alexander Brosius entwickelte makrostrukturierte Tiefziehen umgeht dieses Problem: Statt zwischen zwei flachen, starren Haltern wird das Blechstück zwischen drehbaren Kugeloberflächen eingespannt – wobei die Kugeln im Niederhalter und in der Matrize zueinander versetzt sind, sodass das Blech an jeder Stelle nur entweder mit der oberen oder der unteren Seite im Kontakt ist. «Dadurch lassen sich auch Bleche bearbeiten, die unterschiedliche Dicken aufweisen», sagt Brosius. «Der Herstellungsprozess wird viel flexibler und robuster.»
Einen Nachteil hat der neue, schmelzfreie Prozess: Die produzierten Bauteile werden nicht derart gleichmässig sein, wie konventionell hergestellte. «Sie sehen weniger glatt und eben aus. Sie haben unterschiedliche Dicken und sie haben sichtbare Schweissnähte», sagt Brosius. Im Extremfall bestünden sie aus mehreren Dutzend einzelnen Stahl- oder Aluminiumstücken. Für lackierte Aussenflächen eines Autos eigneten sich solche Werkstücke nicht. «Aber als Trägerstrukturen, bei denen es nicht auf die Optik sondern auf die Stabilität ankommt, taugen sie auf jeden Fall.»
Ein wichtiger Teil des Projekts dreht sich darum, die Eigenschaften der rezyklierten Metallteile gezielt zu verbessern. Diese sogenannte laserbasierte Oberflächenfunktionalisierung ist das Fachgebiet von Andrés Fabián Lasagni. Er entwickelt unter anderem Methoden, mit denen sich Metalle und andere Materialien Wasser-, Schmutz- oder Bakterien-abweisend machen lassen. Dazu ätzt er mittels Laser winzige, nur mikro- oder nanometergrosse Strukturen in die Oberfläche. «Wir können beispielsweise den Korrosionsschutz eines Metallteils erhöhen oder – in der Lebensmittelindustrie – dafür sorgen, dass Oberflächen auf Dauer keimfrei bleiben», sagt Lasagni.
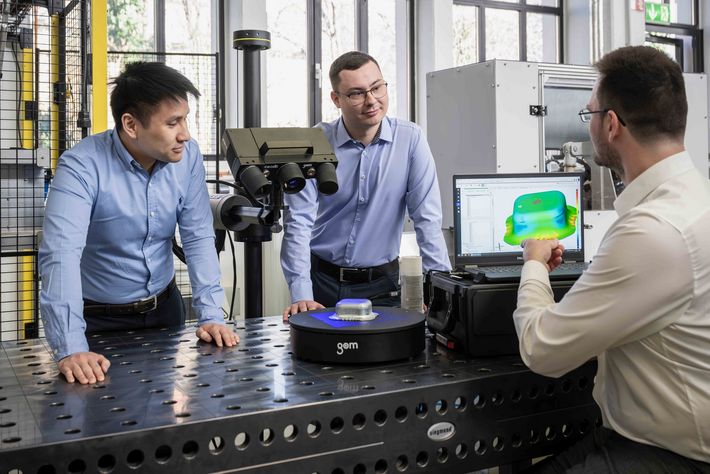
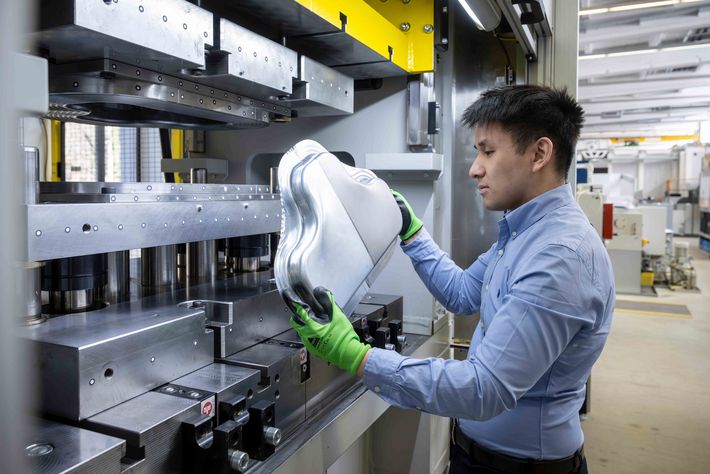
«Ich war einmal ein Porsche»
Dank dieser Veredelungs-Technik geht das Projekt des Dresdner Forschungsteams weit über das reine Metall-Recycling hinaus. «Wir werden Metallbauteile herstellen, die andere, bessere Funktionalitäten aufweisen als die Ausgangsprodukte», sagt Lasagni. Damit, so sind die beiden Forschungsleiter überzeugt, lässt sich der optische Nachteil, der mit dem Verzicht auf das Einschmelzen einhergeht, mehr als wettmachen.
Zumal sie noch ein weiteres Ass im Ärmel haben. Mittels Lasertechniken ist es nämlich auch möglich, die Bauteile zu beschriften oder zu kennzeichnen. Eine nur mikrometergrosse Nut schützt diese Informationen vor mechanischem Abrieb – und sie lassen sich nur mit einer speziellen Software wieder auslesen. Wichtige Informationen könnten die Zusammensetzung, Eigenschaften oder die Herkunft eines Bauteils sein. Auch eher spielerische Anwendungen wären möglich: Eine Idee ist es, auf das «Vorleben» des Metallstücks hinzuweisen: «Ich war einmal ein Mülleimer.» Oder: «Ich war einmal ein Porsche.»
Bei all den zigtausend Metallbauteilen, die auf dem Markt zu finden sind, stellt sich die Frage: Auf welche will sich das Forschungsteam konzentrieren? Das werde sich im Detail erst im Lauf des Projekts zeigen, sagen Lasagni und Brosius. Klar ist aber, dass zuerst eher grössere, einfache und danach immer kleinteiligere, komplexere Bauteile und Kombinationen im Fokus stehen werden. «Wir müssen zunächst schaffen, die Metallbauteile mit unserer Methode herzustellen und dann machen wir sie schrittweise besser», sagt Brosius.
Modellfabrik und Gruppierungs-App
Gleichzeitig stellt sich eine weitere Herausforderung. Soll die Industrie dereinst die neuen Techniken anwenden, reichen Labornachweise nicht. «Firmen wollen sehen, dass unsere Prozessketten für eine Produktion im grossen Massstab geeignet sind», sagt Brosius. Die Forschenden werden deshalb eine Modellfabrik aufbauen – eine Fertigungsstrasse, in der an Beispielen aufgezeigt wird, wie aus bestimmten Ausgangsteilen Schritt für Schritt und automatisiert neue Metallbauteile entstehen. Die Prozesskette sei relativ lang, sagt Andrés Fabián Lasagni. Die Integration und das Zusammenspiel der einzelnen Schritte, also die Planung, werde eine der grossen Herausforderungen des Projekts.
Ein zweiter Forschungszweig, um die Akzeptanz auf dem Markt zu fördern, ist die Entwicklung einer Klassifizierungs-App. «Vereinfacht geht es darum, dass man mit dem Handy in der Hand auf den Schrottplatz geht und Fotos von Altmetallteilen macht, die einen interessieren», erzählt Alexander Brosius. «Die App berechnet dann, was sich aus diesen Stücken Neues fertigen lässt.»
Solche Methoden und Strategien, da sind sich die beiden Forscher einig, werden nötig sein, um ihr Projekt zum Fliegen zu bringen. Denn die Prozesse, die sie zum Upcycling von Metallbauteilen entwickeln, stellen in vielen Belangen heutige Paradigmen der Fertigungstechnik infrage. Gelingt es aber, dem neuen Ansatz zum Durchbruch zu verhelfen, ist es ein wichtiger Schritt, um einen der energieintensivsten Industriezweige nachhaltiger zu machen.
Zahlen und Fakten
Mittel der Werner Siemens-Stiftung
13 Mio. Euro
Projektdauer
2025–2032
Projektleitung
Prof. Dr.-Ing. Alexander Brosius, Professur für Formgebende Fertigungsverfahren, Technische Universität Dresden
Prof. Dr.-Ing. Andrés Fabián Lasagni, Professur für Laserbasierte Fertigung, Technische Universität Dresden
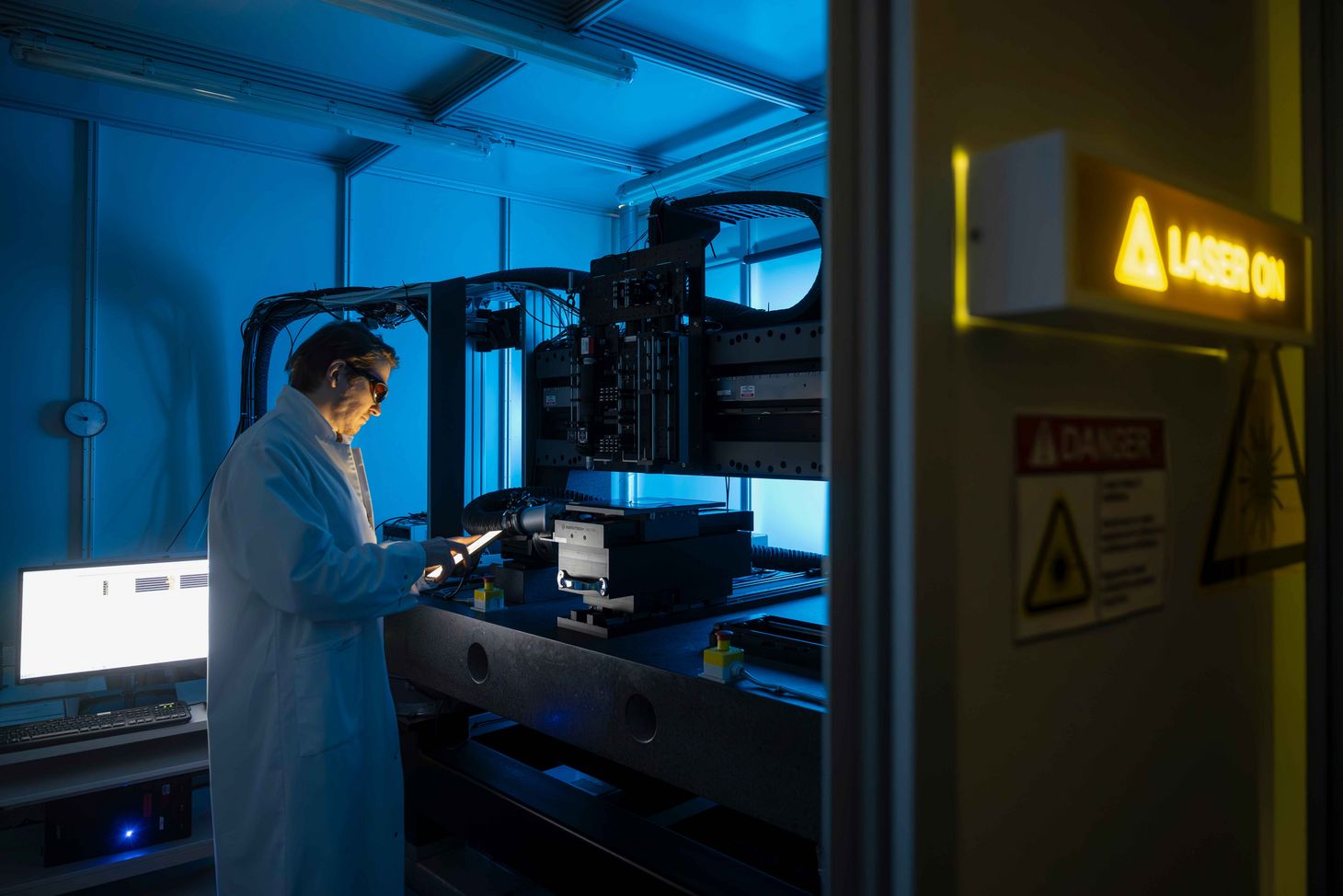