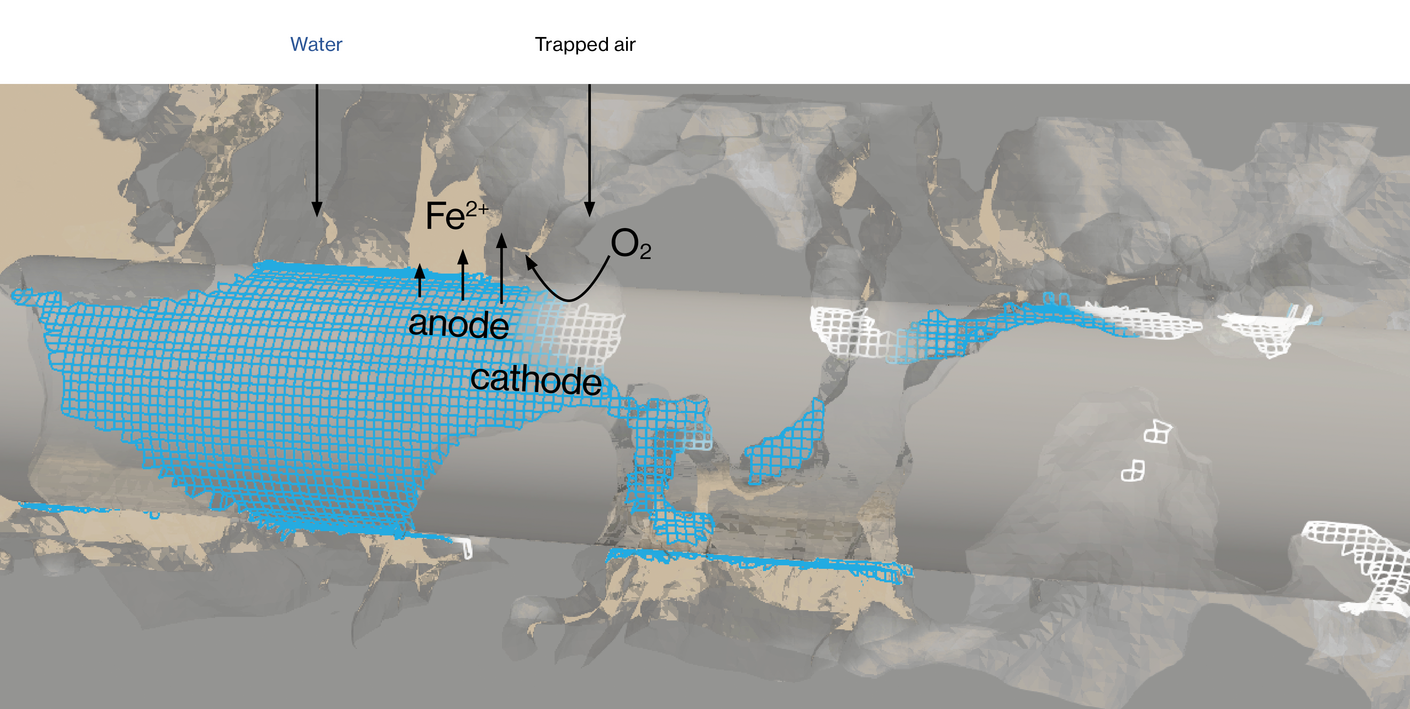
The interior life of concrete
Last year, the team led by civil engineer Ueli Angst studied corrosion processes occurring at the pore level in reinforced concrete. Now they plan to analyse how corrosion unfolds at ever-larger scales—with the aim of developing recommendations and tools for enabling ecological corrosion protection in concrete structures.
ETH professor Ueli Angst and his team approach their research questions from the bottom up, and the first step in their WSS project is examining corrosion processes in reinforced concrete at the nano- and micrometre scale. They want to better understand the most common cause of corrosion—moisture that permeates concrete in the form of rain or spray and that, in the worst case, leads to rusting in the embedded rebar.
Water that penetrates the concrete’s pore system is never pure, and gases—such as CO2—dissolving in the water react with substances like calcium and silicates that are also present in the concrete.
Last year, Angst’s team studied the role silicates play in corrosion and observed the following: the higher the concentration of dissolved silicon, the slower a transformation process between two iron corrosion products will proceed; in addition, the corrosion product with the larger specific volume is stabilised for a longer period of time. “This is a first relevant finding,” Angst says. It’s significant because a slow transformation from “bulky” to “smaller” corrosion products influences how cracking in concrete materialises. Precipitations confined to a small area lead more quickly to stresses in the concrete and eventually cause cracking.
Building knowledge
The corrosion experiments are usually carried out by Ueli Angst’s PhD students in their ETH Zurich labs, but some studies are also conducted at partner institutions: the Paul Scherrer Institute (PSI), the Swiss Federal Laboratories for Materials Science and Technology (Empa) and other labs with specialised infrastructure in Europe and North America. For example, Fabio Furcas, who led the silicate experiment during his doctorate, has taken a postdoc position at Empa, where he’ll continue researching related topics—in collaboration with Ueli Angst. “The process of building up knowledge related to the WSS project is well underway,” Ueli Angst says, expressing his pleasure about the growing research community in the field. Now, his team members are no longer exclusively from materials sciences: they’re also chemists, physicists, chemical engineers and civil engineers.
For the official start of the WSS project in January 2025, Angst is seeking three to four more PhD students. “Apart from the right scientific qualifications, team spirit is a key requirement,” Angst says. “The newcomers should fit in well with our international team.”
Skills in microscopy are a requirement for some of the PhD students, as they’ll be studying the microstructure in concrete with an ion beam device—specifically, a “Focused Ion Beam Scanning Electron Microscopy” or FIB-SEM that enables a 3D visualisation of the concrete’s interior microstructure in the nanometre range.
This makes it possible to conceptualise processes like moisture transport through the fine, intricate pore system and the coupled corrosion processes at the level of the individual pores. “We can finally move away from predominantly empirical testing of specific concrete types—long the traditional approach—and towards attaining a fundamental understanding of corrosion,” Angst says.
With FIB-SEM, the researchers bombard a material sample with a focussed ion beam, thereby removing the smallest layers of the porous material. Layer by layer, they scan the sample with a scanning electron microscope, then use the scans to construct a 3D digital model of the porous material. “We can use the digital model to study various processes, including how a water molecule or iron ions move through the concrete,” Angst says. The resolution in the nanometre range is so high that the effects of capillary forces in the pores are visible.
Models replace individual testing
The imaging technique has the disadvantage of being time-consuming: it takes a good one hundred and twenty hours at the microscope before a “digital twin”—as Angst calls the digital model—is fabricated. But it’s worth the effort, as the digital twin can model a range of scenarios, including a simulation of changes in the pore system of reinforced concrete when it’s exposed to rain, sunshine or temperature fluctuations.
In particular, the team want to find out how capillary forces suck up moisture into the concrete’s pore structures, where it then spreads. “It’s a very dynamic process,” Angst explains. How concrete dries is also fundamental to understanding corrosion—in particular how long residual moisture remains in the pore system.
Ueli Angst envisions that corrosion protection measures can be optimised for a specific environment already when planning a structure. This approach makes sense, as “so many different cement types are developed worldwide that testing them all is simply impossible”, Angst says. “What’s more, established testing methods for new cements and concretes have limited application because they depict processes that, in many new materials, are different to those in traditional concrete.”