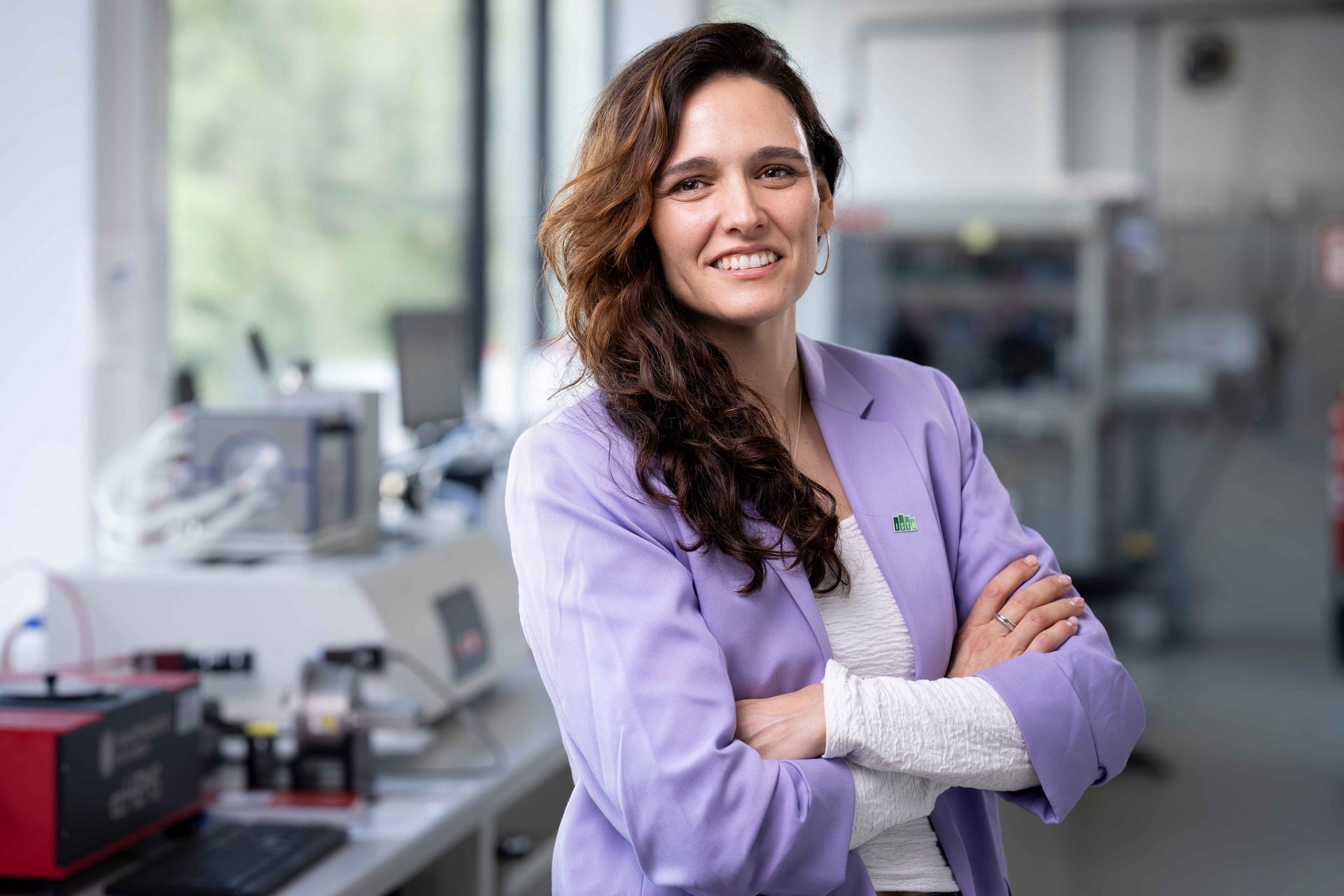
Thermoelectric materials from a 3D printer
Maria Ibáñez and her team at ISTA in Klosterneuburg near Vienna are taking thermoelectric cooling devices to the next level—thanks to their novel 3D printing method to enable the cost-effective fabrication of powerful thermoelectric materials. A publication on their development recently appeared in top-tier journal “Science”.
The principle is ingenious: thermoelectric materials convert temperature differences into an electric voltage and, conversely, use an applied voltage to drive heat transfer. Applications for this thermoelectric effect include both power generation and thermal management—for cooling electronic devices, for example. In the latter case, thermoelectric coolers use an electric current to transfer heat from one side of a device to the other, enabling localised cooling.
If made viable for the massive scale required for industrial application, thermoelectric cooling could replace conventional compressor cooling based on chemicals—a technology with enormous global warming implications. However, considerable science and engineering challenges must be mastered before these devices can be built with the required structural control that ranges from the centimetre to the atomic scale.
Record performance, limited applicability
Previous efforts to exploit the thermoelectric effect have focused mainly on developing high-performance thermoelectric materials. Although these fabrications often achieve record performance and are of scientific value, their scalability is limited due to the high cost of precursor materials, energy-intensive synthesising methods and the complex, expensive and time-consuming machining processes required for shaping ingots into the desired forms for device integration, which also causes significant material waste.
Now, Maria Ibáñez and her group at the “Werner Siemens Thermoelectric Laboratory” at the Institute of Science and Technology Austria (ISTA) in Klosterneuburg near Vienna have developed a solution to these problems thanks to their 3D-printed, thermoelectric materials, which are directly sculpted into the required shape—and that achieve record-breaking performance levels. The researchers, whose work is financed by the Werner Siemens Foundation, recently published a report on their new, innovative and cost-effective approach in prestigious journal “Science” (*).
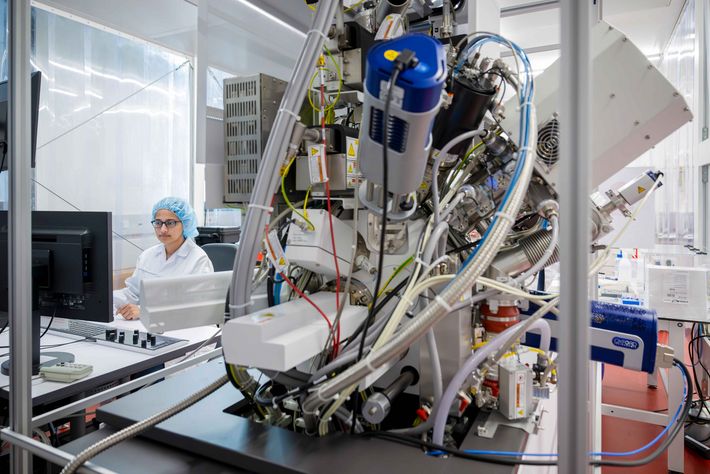
A smart printing strategy
Although various attempts to use 3D printing technology for fabricating efficient thermoelectric materials have already been made, Maria Ibáñez relates, the end-products never matched the performance levels of materials produced using conventional—and costly—methods. “The main reason these previous attempts were unsuccessful is because the particles in the materials failed to bond effectively, thus hindering electron transport,” Ibáñez explains. By contrast, the printing technique developed by her team guarantees this essential bond between particles, hence the production of a well-connected material. “We designed the ink to boost particle bonding and ensure the printed structure stays intact during the evaporation of the solvent,” Ibáñez says.
To create the ink, thermoelectric powder particles consisting of a compound constituted by bismuth, antimony and tellurium, namely Bi2SbTe3, are mixed with a carrier solution and two different types of binders. The ink is then printed out, layer by layer, onto a surface. Then, the printed structure is heated, causing the carrier solution to evaporate. Due to the properties of the binders chosen, the particles are bonded and the structure retains its integrity. This highly effective bonding is made possible because the heat sets off a chemical reaction between the two binders, causing the previously loose particles to form strong chemical bonds, but without changing the overall material composition. The creation of a well-connected material network in a porous structure prevents heat from passing through very well while still allowing electricity to flow easily, which is precisely what thermoelectric materials must do.
High performance, low cost
With their method, the researchers created high-quality materials with a thermoelectric performance numbering among the highest ever observed at room temperature. To demonstrate the practical potential of the 3D printed materials, they printed thermoelectric pillars and integrated them into a device, whose cooling capability was then tested. This is the first instance of 3D-printed materials being used to fabricate a thermoelectric cooler, and the method overcomes significant challenges in material optimisation and device engineering.
“Our devices exhibit a net cooling effect of fifty degrees in air,” says Shengduo Xu, postdoc in Maria Ibáñez’s group and lead author of the study. “It’s the first 3D-printing-based thermoelectric cooler whose performance is comparable to that of conventional, ingot-based devices that, for decades, have been built and further developed in industry using costly and inefficient methods.”
Maria Ibáñez is convinced her team’s approach has broader implications: “Our work represents a general, more widely applicable methodology for 3D-printed functional ceramics.” What’s more, she adds, the ISTA findings shouldn’t be seen only as a significant contribution to the field of thermoelectrics: they’re also relevant to 3D printing technologies for semiconducting materials and emerging research: “The potential impact on the future of electronics is huge.”
(*) Article in “Science”
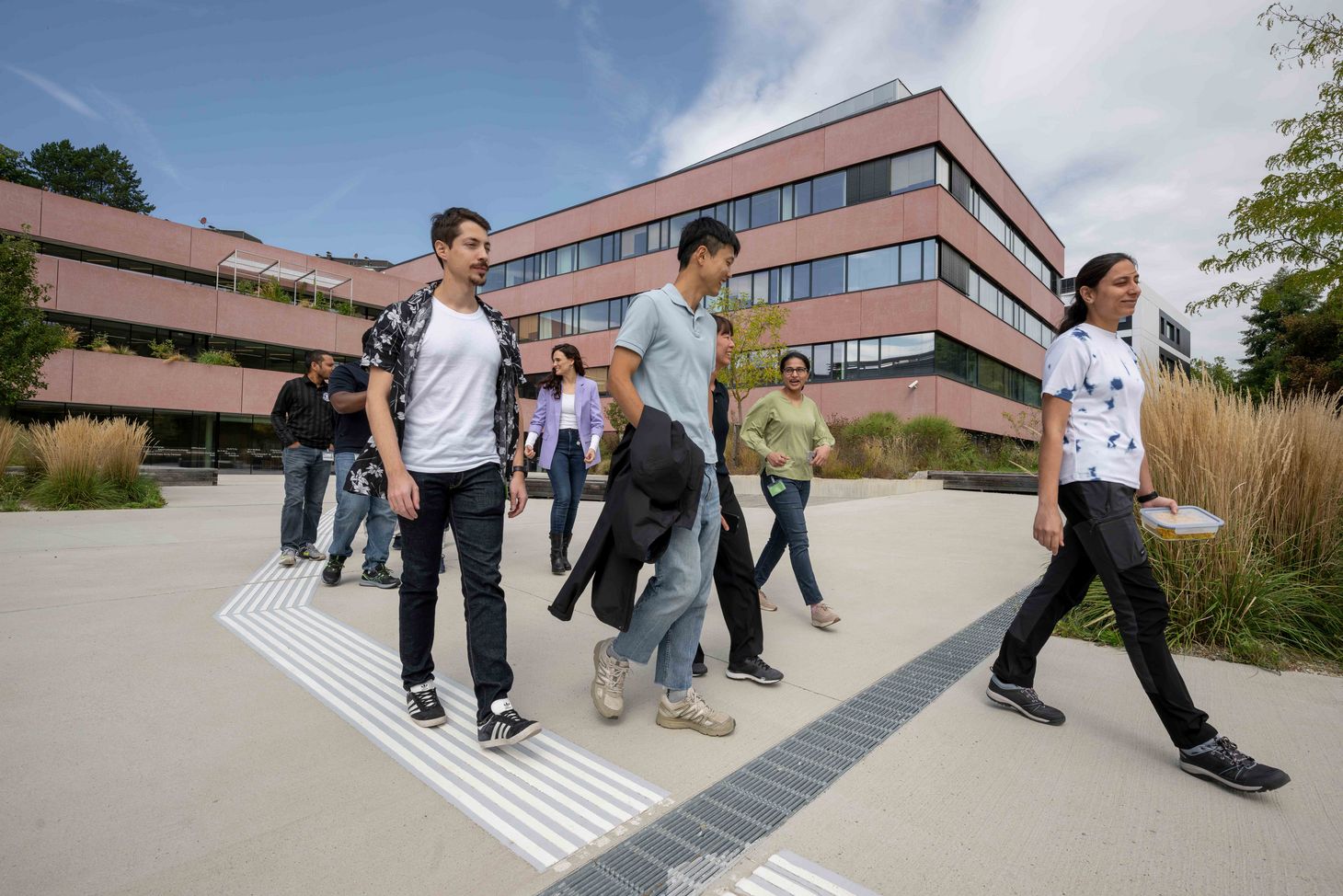